
The Top 10 OSHA Violations and How to Avoid Them
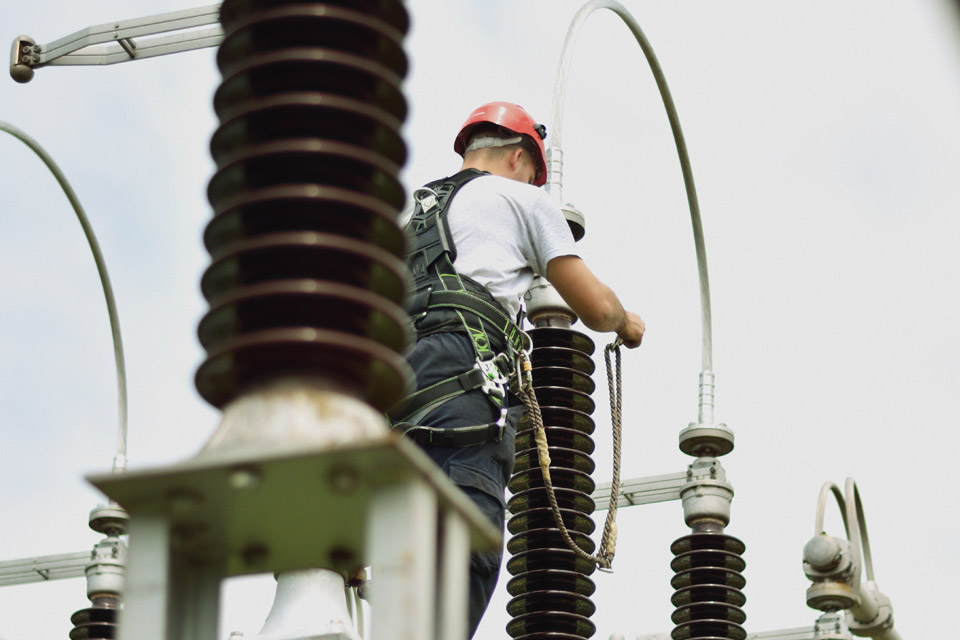
The Occupational Safety and Health Administration (OSHA) is the federal agency in charge of monitoring workplace safety, enforcing safety procedures, and issuing citations and fines to businesses that violate safety regulations. An employer commits OSHA violations when they repeatedly or intentionally disregard the Occupational Safety and Health Act requirements, also known as the OSH Act, and fail to ensure that their workers are in a safe environment at work.
This article lists the ten most common OSHA violations and discusses strategies to avoid them.
Top 10 OSHA Violations
1. Fall Protection (General Requirements)
Meeting fall protection requirements set by OSHA standard 1926.501 is crucial to ensure the safety of workers at risk of falling from heights. It includes safety requirements related to fall protection, such as what protection systems are necessary and where to use them.
Strategies for meeting fall protection requirements include the following:
- Identify areas with potential fall hazards in your workplace.
- Determine the right fall protection measures based on the type and height of work performed.
- To prevent falls, install guardrails along open-sided platforms, walkways, ramps, and runways.
- If guardrails are not possible, use personal fall arrest systems (PFAS) such as harnesses, lanyards, and anchor points, and install safety nets.
2. Fall Protection (Training Requirements)
OSHA standard 1926.503 outlines training requirements for fall protection. This section requires companies to supply adequate worker safety training to anyone exposed to fall hazards.
Ways to avoid violating these training requirements include the following:
- Figure out which OSHA standards apply to your workplace based on the industry (construction or general industry) and the type of work.
- Create a comprehensive fall protection training program covering your workplace’s specific hazards and the relevant OSHA requirements.
- Include information on the nature of fall hazards, fall protection systems, and equipment, proper use of equipment, rescue procedures, and the employer’s fall protection plan.
- Ensure qualified personnel with the knowledge and expertise to communicate fall protection concepts and practices conduct the training.
3. Respiratory Protection
OSHA standard 1910.134 covers respiratory protection, from designing worksite protection programs to respirator use and maintenance.
Avoiding a respiratory protection violation includes the following steps:
- Identify workplace areas and tasks that may expose employees to airborne contaminants.
- Decide the types and levels of respiratory hazards present and the duration and frequency of exposure.
- Choose the proper respirator type based on the hazards and levels identified in the hazard assessment.
- Conduct fit testing for tight-fitting respirators to ensure a proper seal on the wearer’s face.
4. Hazard Communication
OSHA standard 1910.1200, also known as HazCom, covers chemical hazards, including those produced in the workplace and imported from outside locations, and hazard communication standards (how employers communicate the potential dangers to employees).
Strategies for avoiding a hazard communication violation include:
- Create a comprehensive inventory of all hazardous chemicals used, stored, or produced in the workplace.
- Identify each chemical and its associated hazards, such as physical, health, and environmental risks.
- Lebel all hazardous chemicals are correct with accurate and easily understandable information.
- Obtain Safety Data Sheets (SDSs) from chemical manufacturers, importers, or distributors for each hazardous chemical.
5. Ladders
OSHA standard 1926.1053 is a general requirement for safe ladder use in the workplace.
Companies should consider the following steps to avoid a ladder violation:
- Choose the right type and size of ladder for the task at hand. Consider factors such as ladder length, load capacity, material, and the environment in which it will be used.
- Allow employees adequate room to step down from the ladder safely.
- Regularly inspect ladders before each use for any visible defects, such as cracks, broken rungs, missing parts, or damaged rails.
- Maintain three points of contact (two hands and one foot or two feet and one hand) while climbing up or down a ladder.
6. Scaffolding
OSHA standard 1926.451 covers safety requirements related to scaffolding.
Avoiding scaffolding-related violations includes the following steps:
- Ensure that competent and qualified personnel design, erect, and construct scaffolds.
- Provide safe access to and from scaffolds, including stair towers, ladders, or other approved means.
- Inspect scaffolds before each work shift and after any alterations or adverse weather conditions that could affect stability.
- Equip suspended scaffolds with fall protection, including guardrails and personal fall arrest systems.
7. Powered Industrial Trucks
OSHA standard 1910.178 covers powered industrial trucks on worksites, like forklifts and motorized hand trucks, including their operator training and maintenance.
To avoid a violation related to powered industrial trucks:
- Ensure the proper training and certification of operators of powered industrial trucks.
- Establish and enforce safe operating procedures for powered industrial trucks, including proper mounting and dismounting, turning, maneuvering, and load handling.
- Conduct pre-shift inspections of powered industrial trucks to identify any defects or malfunctions.
- Establish traffic management plans to prevent collisions and near misses between powered industrial trucks and other vehicles, pedestrians, or equipment.
8. Control of Hazardous Energy (Lockout/Tagout)
OSHA standard 1910.147 covers the control of hazardous energy. It outlines the necessary performance requirements to safeguard employees from unexpected energization, such as the release of potentially dangerous stored energy or sudden machine startup.
To properly control hazardous energy on your worksite:
- Find all sources of hazardous energy that need control during maintenance or servicing.
- Designate and train authorized employees responsible for implementing lockout/tagout procedures.
- Use lockout devices (such as padlocks) to prevent equipment energization physically.
- Use tags only when lockout devices are unapplied due to limitations in use.
9. Eye and Face Protection
OSHA standard 1926.102 covers using personal protective equipment (PPE) to safeguard workers from hazards that could cause eye or facial injuries.
To provide proper eye and face protection:
- Choose suitable eye and face protection equipment that supplies adequate coverage and protection based on the identified hazards.
- Ensure that the selected eye and face protection equipment fits comfortably and securely.
- Inspect eye and face protection equipment for damage, scratches, or other visibility and protection issues.
- Keep eye and face protection equipment clean and free from dirt, debris, or substances impairing visibility or irritating skin.
10. Machine Guarding
OSHA standard 1910.212 discusses how to guard machinery and equipment to shield operators and other onsite employees from potential dangers.
Steps to avoid a violation related to machine guarding include the following:
- Choose the proper type of machine guarding based on the specific hazards associated with each machine.
- Machine guards should be either fixed to the machine or otherwise secure if they can’t be attached directly.
- Ensure that guard designs prevent workers from reaching the hazard zone or contacting moving parts.
- Regularly inspect machine guards to ensure they are in place, properly adjusted, and not damaged.
Avoiding OSHA Violations is Critical for Keeping Workers Safe
Understanding and knowing how to prevent OSHA violations helps companies protect workers and avoid costly OSHA penalties and fines. Connect with us to learn more about how you can protect your business and your workers by leveraging a comprehensive contractor management solution to meet your needs.