
Rethinking Zero: Why All Incidents Are NOT Preventable, but Fatalities Can Be
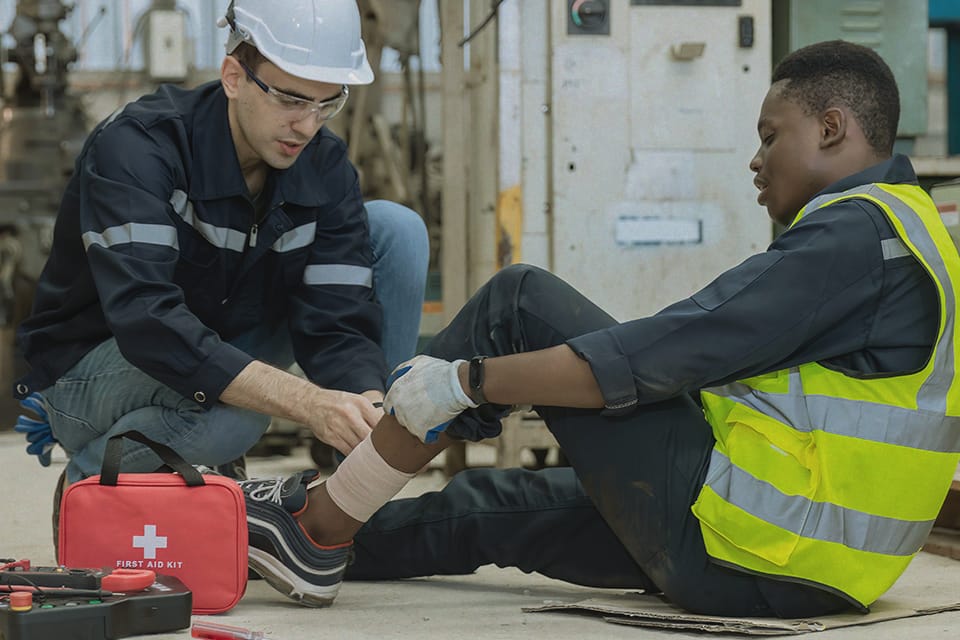
For decades, the safety industry has rallied around the idea of “zero incidents,” with Total Recordable Incident Rate (TRIR) as the gold standard for safety performance. While well-intentioned, this philosophy has created a mindset that often ignores the complexity of humans and the realities of high-risk work environments. Fatality rates staying the same each year is a clear indication that lower TRIR isn’t the answer.
This article challenges the long-held belief that “all incidents are preventable” and argues for a more focused, proactive approach that measures what we can control.
No fatalities through strict adherence to Life-Saving Rules and Critical Safeguards should be at the forefront of every safety program. Companies that actively assess the “maturity level” of their safety programs are the ones making a difference! Is your company lucky or do you have “ALL” safeguards in place to prevent fatality when an incident occurs?
The Myth of Zero Incidents
The idea that all workplace incidents are preventable has become a cornerstone of many safety programs. It is a powerful message: simple, optimistic, and easy to communicate. But it is also misleading. Years of incident data, and real-world experience tell us a different story.
Humans are fallible, and even in the most controlled environments, mistakes happen. The pursuit of a TRIR of zero can unintentionally lead to underreporting, blame culture, and misplaced focus on minor injuries rather than the prevention of Serious Incidents or Fatalities (SIFs).
The Data Does Not Lie: Incidents Still Happen
If you analyze the data, it shows injuries occur even in high-performing organizations. No amount of training, automation, or policy will eliminate the human element. People get distracted, make judgment errors, misinterpret procedures, take shortcuts under pressure, or get put in tough situations without a safe option.
These behaviors are not always signs of negligence; they are part of being human. Safety systems must be designed with this in mind, not in denial of it. Fail safes should be built into the work so that when an employee makes a mistake, the likelihood of a SIF is minimized.
The Problem with TRIR Obsession
Focusing too heavily on TRIR can lead to:
- Underreporting of minor injuries to protect KPIs
- Overreaction to low-severity incidents
- Neglect of high-risk, low-frequency hazards
- Distrust between frontline workers and management
This creates an approach where safety becomes about numbers, not people. In fact, organizations that report zero incidents over extended periods often do so by redefining or underreporting what qualifies as a recordable injury. This undermines the integrity of safety programs and shifts the focus away from what truly matters of preventing life-altering and fatal events.
The Real Goal: No Fatalities
Instead of chasing the illusion of zero incidents, organizations should aim for no fatalities. A goal that is both morally imperative and operationally achievable. Fatalities are generally linked to specific high-risk activities that are governed by Life-Saving Rules (LSRs). When these rules are followed, audited, and enforced, the likelihood of a fatal event drops dramatically.
Life-Saving Rules: The Foundation of Fatality Prevention
LSRs are non-negotiable behaviors and controls that address the highest risks in the workplace. Examples include lockout/tagout procedures, confined space entry, and fall protection.
Organizations with advanced safety maturity will embed LSRs into daily operations by modeling strong leadership, fostering a mindset of accountability focused on learning, providing effective training, and conducting audits that aim to resolve issues rather than assign blame.
Safeguards First, Metrics Second
Before focusing on metrics like TRIR, companies must ensure that critical safeguards are:
- Identified through risk assessments
- Implemented with engineering and administrative controls
- Audited regularly for effectiveness
- Maintained and updated as conditions change
Only once these safeguards are in place and functioning should your attention turn to recordable injuries and even then, with the understanding that not all recordables are equal in severity or preventability. You may be surprised to see that shifting the focus to SIF prevention can directly contribute to a reduction in TRIR.
Shift the Focus, Save Lives
It’s time to shift the safety conversation toward a more realistic and practical approach to incidents. When field employees hear phrases like, “all incidents are preventable,” in safety meetings, they often disengage because it doesn’t reflect the complex realities they face on the job. History shows that all incidents are not preventable, and pretending otherwise sets organizations up for failure.
Measuring “safety culture” through surveys isn’t going to get you the answers you want either, this measures the employees. Companies need to look inwards and assess their maturity level towards safety. A shift from safety culture to safety maturity is paramount. “Culture” implies a fixed state, employees either have it or they don’t where “maturity” sees safety as a journey with clear stages of growth. Maturity can also be measured based on programs and systems. It is time to start talking about the “maturity” level of your safety program as opposed to the “culture.” Here are a few highlights of a “mature” safety program:
- Fatal risks clearly identified, talked about, and controlled. They don’t just rely on luck.
- LSRs are non-negotiable no matter what the schedule demands.
- Leaders prioritize learning over blame; they ask better questions to learn why.
- Workers feel safe reporting near misses and minor injuries.
- Metrics support; they don’t drive safety decisions.
Recommendations
1. Reframe safety goals: Replace “zero incidents” with “no SIFs.”
2. Audit life-saving rules: Regularly verify implementation, compliance and effectiveness of safety systems before work starts. Don’t just talk about them.
3. Train for high-risk scenarios: Focus on the activities most likely to result in fatal outcomes and prepare.
4. Encourage reporting: Create a culture where all incidents and near misses are seen as learning opportunities and TRULY mean it. How companies respond determines if that employee reports again.
5. Use TRIR wisely: Treat it as one of many indicators, not the ultimate measure of safety performance.
6. Measure company safety maturity: Take a deep dive into the maturity level of company safety programs to accurately measure and take action where needed.
About the Author
Chris Court, MPH, CSP, has over a decade of experience leading health, safety, and environmental initiatives across high-risk sectors including construction, energy, petrochemical, and manufacturing. As a Senior HSSE Leader at Zachry Group, Chris currently oversees safety operations for one of the largest LNG export facilities in North America, managing a team that peaked at 150 HSSE professionals that supported a workforce that topped at 15,000.