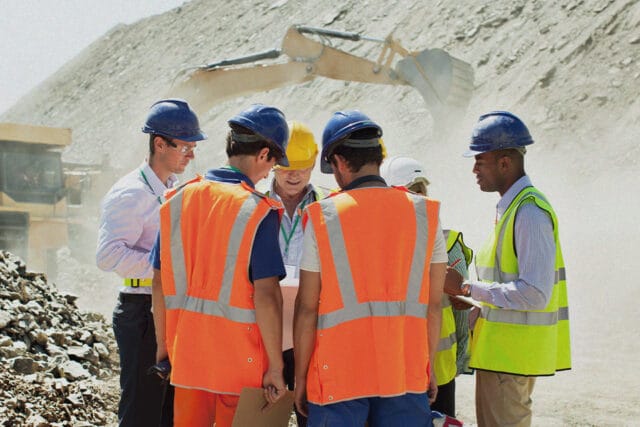
Behavior-Based Safety Essentials for Upstream Oil and Gas
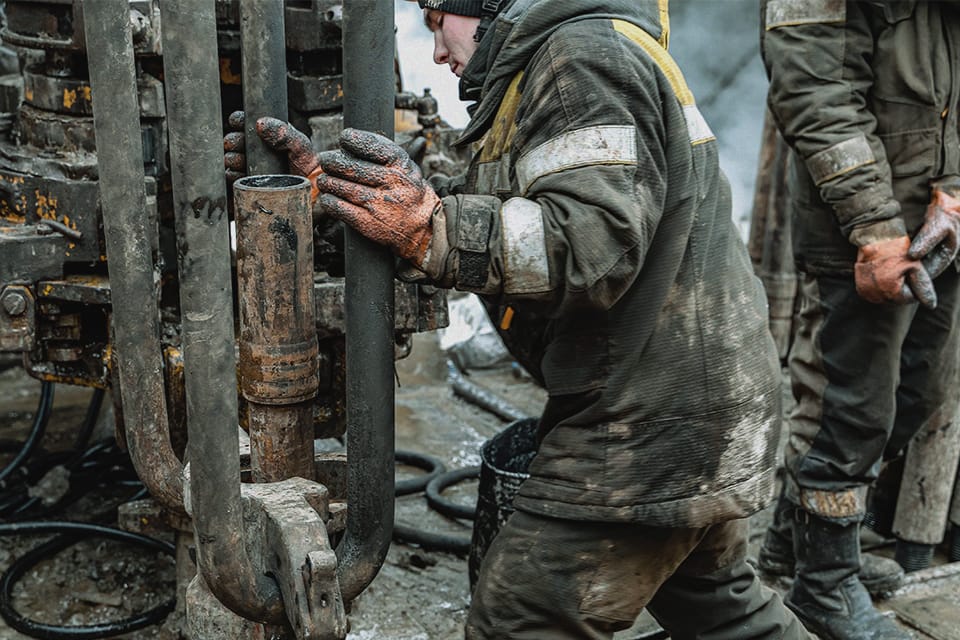
Exploring the realm of behavior-based safety opens a new chapter in ensuring upstream oil and gas safety. It’s no longer about going through the motions or sticking strictly to a script; it’s more about nurturing an atmosphere where each person on the team is encouraged and feels empowered to chip in towards making our workspace as safe as possible.
With reports indicating that companies with effective behavior-based safety programs see significant reductions in injuries, understanding and implementing these practices has never been more critical.
This article discusses the basics of behavior-based safety, its benefits in upstream oils and gas, and how to implement the best program.
What is Behavior-Based Safety?
Behavior-based safety (BBS) is a proactive approach to improving workplace safety. It focuses on identifying and reinforcing safe ways of behaving while discouraging unsafe conduct.
The goal is to create a safety culture where employees are actively engaged in promoting safe work practices. And let’s not forget, cutting down on the chance of accidents and injuries is important, too.
The first step in implementing a BBS program is to identify the critical safe behaviors that need to be observed and reinforced. They should be specific, observable, and measurable.
Once the critical behaviors have been identified, trained observers conduct regular observations. They record the frequency of safe and at-risk actions. The data collected during these observations is used to provide feedback to employees and track progress over time.
Positive Feedback Is Essential to BBS
Positive reinforcement is a key component of behavior-based safety. When employees are recognized and rewarded for demonstrating safe behavior, they’re more likely to continue those behaviors in the future.
This can be done through verbal praise, written recognition, or small rewards. By focusing on positive reinforcement rather than punishment, BBS programs create a more supportive and collaborative safety culture.
Benefits of Implementing a BBS Program
Reduced Downtime
One of the primary benefits of implementing a BBS program is reduced downtime due to accidents and injuries. When companies get ahead of the game by spotting and fixing risky behaviors, they can stop accidents in their tracks before anyone gets hurt.
This not only keeps workers safe but also lessens the disruption to production that accidents and investigations cause.
Improved Morale
Behavior-based safety programs can also lead to improved employee morale and job satisfaction. When workers feel that their safety is a top priority and that their input is valued, they’re more likely to be engaged and committed to their work.
BBS programs encourage open communication and collaboration between workers and management. This fosters a sense of teamwork and shared responsibility for safety.
Encouraged Efficiency
By focusing on safe conduct and eliminating at-risk behaviors, BBS programs can also encourage greater efficiency in the workplace. Workers can concentrate more intently on their tasks when unsafe conditions or practices are not distracting them.
This can lead to increased productivity and quality, benefiting both the company and its employees.
Enhanced Quality
In addition to improving efficiency, BBS can also enhance the quality of work produced. When workers aren’t rushing or taking shortcuts to meet deadlines, they’re more likely to pay attention to detail and follow proper procedures.
This can result in fewer defects, less rework, and higher customer satisfaction.
Key Concepts of Behavior-Based Safety
The ABC Model
The ABC (Antecedent-Behavior-Consequence) model is a foundational concept in behavior-based safety. It asserts that both the events that come before behaviors and the results that follow them (antecedents) have an impact on them.
When safety pros get a handle on these elements, they’re in a great spot to boost safe actions and put the brakes on the risky ones. Antecedents might include training, safety equipment, or job site conditions. Depending on the situation, outcomes might range from a pat on the back and words of encouragement to some constructive pointers or even a more serious chat about what needs to change.
Micro Approach vs Macro Approach
Behavior-based safety programs can take either a micro or macro approach. The micro approach focuses on individual actions and provides one-on-one feedback to workers based on observations.
The macro approach looks at broader organizational factors such as management commitment, employee involvement, and safety culture. Most successful BBS programs incorporate elements of both approaches to create a comprehensive safety strategy.
How to Implement a Behavior-Based Safety Program
Secure Buy-In and Pick Your BBS Team
The first step in implementing a behavior-based safety program is to secure buy-in from management and employees. This involves communicating the benefits of BBS, addressing concerns, and involving workers in the planning process.
Once buy-in is achieved, the next step is to select a dedicated BBS team to lead the effort. So, make sure your team is a colorful mix of folks from various parts and levels within the company, including frontline workers, supervisors, and safety professionals.
Collect and Review EHS Data
Before launching a BBS program, it’s important to collect and review existing environmental, health, and safety (EHS) data. This includes accident reports, injury logs, near-miss incidents, and workers’ compensation claims.
Analyzing this data can help identify trends, high-risk areas, and potential targets for behavior-based interventions. It also provides a baseline for measuring the impact of the BBS program over time.
Create a Critical Behavior Checklist
Once the BBS team has reviewed the EHS data and identified potential focus areas, the next step is to create a critical behavior checklist. This checklist should include specific, observable behaviors linked to identified safety risks.
The checklist should be developed with input from frontline workers who have firsthand knowledge of the job tasks and associated hazards. The final checklist should be clear, concise, and easy to use during observations.
Track and Measure Behavior
With the critical behavior checklist in hand, the BBS team can begin conducting regular observations to track and measure behavior. Observers should be trained in how to use the checklist, provide feedback, and record data.
Observations should be conducted at various times and locations to get a representative sample of behaviors. The data collected during observations should be compiled and analyzed regularly. This helps identify trends, measure progress, and make program adjustments as needed.
Combine A New BBS Program with the Right Risk Management Solutions
Embracing behavior-based safety isn’t about turning upstream oil and gas worksites into fortresses against risk but enabling everyone to be guardians of their own and others’ well-being. Gone are the days when responsibility lay solely on the shoulders of designated health officers or management teams.
However, fostering the best safety culture requires more than a BBS program. Management must also integrate the industry’s best risk management solutions to help enforce better behaviors and encourage continuous safety improvement.
Consider partnering with us to configure a solution to complement your behavior-based safety program and protect your onsite workers from the dangers specific to upstream oil and gas.
Contact us today to learn more.