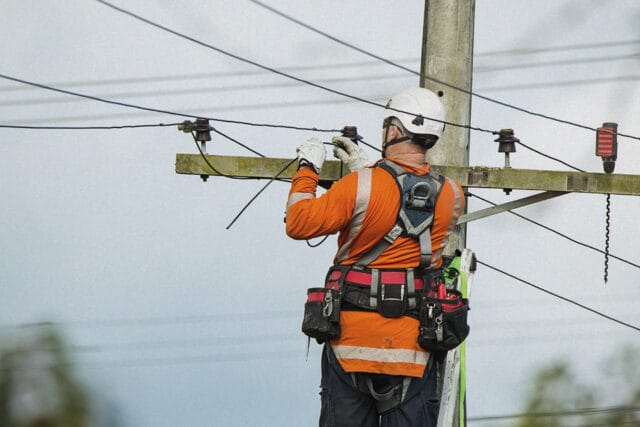
7 Steps to Help Hiring Clients Navigate the Gray Area of Contractor Safety
Making an exception is often a reality when hiring a contractor. Despite intention to adhere to your company’s contractor safety program, highly-specialized, last-minute, or high-volume work demands can quickly leave you in a gray area—unable to find a contractor who meets your company’s safety prequalification requirements or has time to get up to speed with them. An exception management process – that is, a clearly defined plan that allows you to make hiring exceptions – enables you to avoid disruption and get work done as quickly and as safely as possible.
Here are 7 steps for hiring clients to create an exception management process, or enhance one that is already an important component of your company’s contractor safety program. A strong, well-communicated process will enable you and your team to proactively mitigate risk, protect your company’s reputation, and highlight the need for corrective actions or alternative hires. Rest assured, technology is here to help:
1. Define “Approved” Contractor
Before implementing an exception process, you need to ensure that your company’s contractor safety prequalification program clearly defines an approved contractor versus one that requires an exception. The determination is inherently linked to a contractor’s safety performance data, such as OSHA and other safety stats, as well as the contractor’s written safety program. All of this information is gathered and reviewed, resulting in an approved or unapproved status. For example, in the Veriforce program, a safety score is calculated for each contractor that translates to a letter grade that is used by the hiring client’s organization to determine hiring eligibility. A contractor who earns a safety grade of an A or B qualifies for approved status, while one whose safety metrics translate to a C, D, or F safety score would be marked as unapproved and would require an exception.
2. Identify Authorized Approvers and Approval Process
An approval process for exception requests is critical to smart hiring and will enable you to accommodate diverse hiring needs, such as when a job calls for high-risk, remote or location-specific, or longer-term work that may require multiple approvals to mitigate risk.
Typical approval structures for exception requests include senior safety professionals— those who have expertise to review the data and other details behind safety scores and recommend potential risk mitigation requirements—or committee reviews that include representation from safety, supply chain, operations, and sometimes legal or risk management departments. Approval processes should also take into consideration unique circumstances, including those that may require additional approval, such as sign-off from a vice president.
3. Set Controls
A best practice is to implement tight controls over exception hiring. Rather than a broad approval, grant exceptions only on a project-specific basis and clearly define time limits, including an expiration date that requires approval of a new exception request if a contractor needs additional time to complete a project.
4. Install Guardrails
Put in place risk mitigation requirements that will alleviate potential risks associated with a hire that has a questionable safety record. Risk mitigation requirements may include mandatory additional safety training for contractor personnel, the presence of a safety professional (either from the contractor’s staff or yours) when an exception hire is on a job site, or the use of onsite safety audits. It’s also key to define how those with authority to grant exceptions will be required to document their decisions such as clearly capturing what they concluded from their review of the contractor’s safety record and what risk mitigation requirements are mandated as a result. In some cases, a contractor’s poor safety score may be due to an unavoidable incident (e.g., another driver was at fault for hitting a contractor’s employee) that can be explained to allow use of the contractor without with the need for additional risk mitigation requirements.
5. Identify and Share Valuable Data
Data related to exception hires is valuable to you as a safety professional and to your organization’s reputation and bottom line. Useful data to track may be related to location, types of work, or requestor. Assign ownership to your contractor safety program director or someone else in your organization who can analyze the data to spot trends that require action, such as providing additional safety tools and coaching to help an essential contractor reach approved status, or reevaluating the use of a contractor with a consistently poor track record. Data reports should be shared regularly, often monthly or quarterly, to a predetermined set of stakeholders.
6. Get the Word Out
Critical to the success of your new exception process is your ability to clearly define what you have created and to share it with personnel in the field, including project managers, so that existing and new staff can quickly and easily access and follow guidelines when an exception is needed. Oftentimes, your exception management process is best suited for inclusion in documentation related to your company’s contractor safety prequalification process, as it is an integral component of a program that allows you to balance the objectives of mitigating contractor risk, while also minimizing potential project delays or work stoppage when an exception hire is required.
7. Rely on Technology to Implement and Manage with Ease
You undoubtedly leverage technology to manage your contractor safety program, whether via a third-party solution, internally-built system, or a simple Word or Excel document.
A technology solution that integrates exception management into your contractor safety program will provide you with a centralized, web-accessible place to manage all safety-related information and to mitigate risk. Stakeholders in your organization can access and verify where exceptions have been granted and what mitigation may be required (e.g., must a safety professional be on-site while the contractor is working?).
The real-time visibility it offers will also provide a clear audit trail for all exception decisions and associated documentation, allow communication and status updates between requestor and approver, and enable you to use reporting to identify deeper insights and trends that can help to drive ongoing improvements in contractor safety.
Sign up for the latest company updates, knowledge center resources, and more, delivered right to your inbox.
Sign Up for the Latest Updates