
What is a Process Hazard Analysis (and How to Conduct One)?
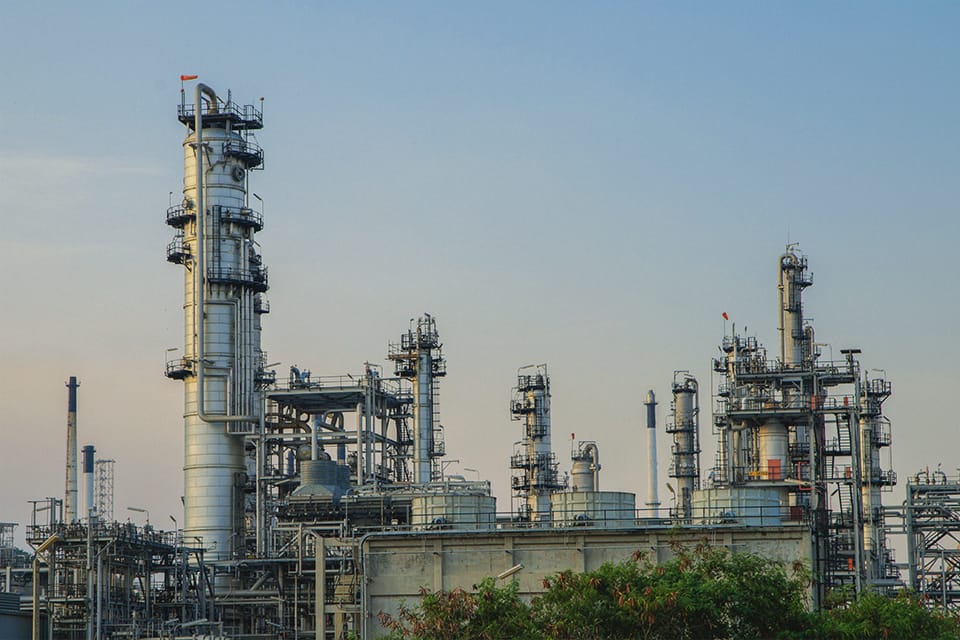
Working in the downstream sector of the oil and gas industry entails significant risk and can often put workers in harm’s way. Good project planning and a process hazard analysis can lower risks and keep everyone safe on-site during execution.
A process hazard analysis helps identify potential risks and the necessary controls to establish. It provides recommendations for mitigating those identified dangers before work begins, helping to keep workers safe. Downstream oil and gas companies must understand these analyses and choose the best method for their operations.
This article defines the process hazard analysis, describes the available methods, and lists the steps to complete one.
What is Process Hazard Analysis (PHA)?
Process hazard analysis (PHA) is a rigorous and systematic approach to determining, assessing, and managing the risks associated with hazardous chemical processes. The relevant consequences might include:
- Worker safety
- Public safety
- Environmental impacts
- Property and equipment damage
The analysis identifies the factors contributing to these incidents and ranks each scenario according to frequency and severity.
What are the Different PHA Methods?
There are several methods for conducting a process hazard analysis, each with strengths and weaknesses. The most commonly used methods are the following:
Hazard and Operability Study (HAZOP)
HAZOP is an organized and systematic procedure for identifying potential process hazards. The process entails the participation of a group of specialists who methodically scrutinize every component and detect possible deviations from the intended operation.
Layer of Protection Analysis (LOPA)
LOPA is a method used to evaluate how well different layers of protection prevent and reduce risks. It assesses their effectiveness in preventing hazards. The process includes:
- Identifying risks
- Considering their likelihood and potential outcomes
- Evaluating the effectiveness of existing safety measures
What-If Analysis
As a qualitative method, the What-If Analysis entails the formulation of hypothetical situations and the examination of their respective repercussions. Evaluating the efficacy of existing controls and identifying potential hazards in this manner is a straightforward and efficient process.
Fault Tree Analysis (FTA)
FTA is a top-down methodology used to identify the causes of prospective system failures. The process entails constructing a logical diagram illustrating the interconnections among the initiating event, system components, and potential failure modes.
Failure Modes and Effects Analysis (FMEA)
FMEA is a quantitative method that identifies potential failures and their consequences by examining each system or process component. The evaluation starts with a diagram showing parts that could malfunction and make operations unsafe.
Hazard Identification (HAZID)
Hazard Identification (HAZID) is a qualitative methodology utilized to identify and evaluate the probability and repercussions of prospective hazards. This method identifies potential risks in a process. It assesses the likelihood of these risks occurring and the possible consequences.
Event Tree Analysis (ETA)
ETA is a bottom-up methodology utilized to assess the prospective repercussions of an occurrence. The process of creating a logical diagram illustrates the potential consequences of an occurrence along with the corresponding probabilities.
Bow Tie Analysis
Utilizing a visual approach, Bow Tie Analysis identifies prospective hazards, their underlying causes, and the repercussions associated with each risk.
The engineers will use this method to make a diagram resembling a bow tie. The diagram will display the causes of potential dangers on one side and the potential outcomes on the other.
Checklist-Based Hazard Analysis
This systematic approach identifies potential hazards and the risks associated with them through protocols. It encompasses significant categories of hazards and risks pertinent to the process within the enumeration.
7 Steps for Conducting a Process Hazard Analysis
1. Establish the Goals and Limits
Before commencing a PHA, management must establish the analysis’s goals and limits. In this process, they will define goals, team members, and the process they will analyze.
2. Choose the Best PHA Method
As discussed above, several PHA methods are available. The best option depends on the complexity of the process, the level of detail required, and industry standards.
Management should select a methodology that aligns with the objectives and available resources.
3. Identify the Hazards
The team finds all possible dangers, like malfunctioning equipment, external factors, and human error.
4. Assess the Risks
After identifying the hazards, the team evaluates the risks linked to each hazard. In this exercise, they determine the likelihood and severity of each danger. They also assess the effectiveness of current safety measures.
5. Create Mitigation Steps
The team creates and establishes safety measures based on risk assessment results to lower the dangers linked to hazards. This involves applying procedures, providing training, or installing safety systems.
6. Document the PHA
The team should create a report to share findings with stakeholders, which is essential for future safety evaluations. The team needs to fully understand OSHA rules and other laws in dangerous workplaces. This knowledge is crucial for safety.
7. Conduct Ongoing Reviews and Updates
Finally, the team regularly checks and updates the PHA to ensure it handles process risks well.
Combine Your Process Hazard Analysis with the Industry’s Risk Management Solutions
Process hazard analysis is necessary for identifying and addressing potential hazards in processes. Oil and gas companies can keep their workers safe by doing a thorough PHA to prevent harm and damage to operations. They can also choose from different PHA methods and pick the one that suits their needs best and keep their processes safe.
However, a PHA alone won’t keep workers safe. Management must also integrate a process safety management solution that offers chemical training to meet safety standards, maintain compliance, and promote a more robust safety culture.
Consider partnering with us to configure that solution and protect your workforce from the risks of handling hazardous substances.
Contact us today to learn more.