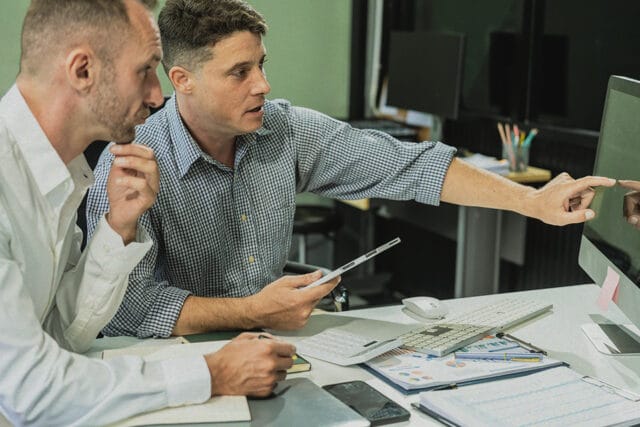
Hazard Communication: 6 Steps to Implementing the Best Plan
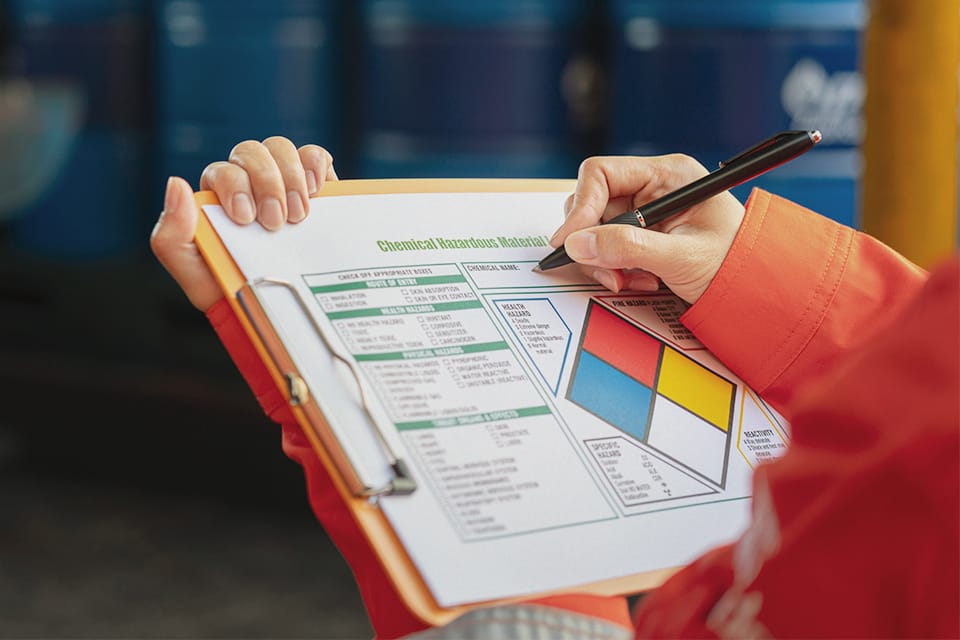
Hazard communication is critical to safety in any environment involving dangerous substances, where workers can face various risks. As such, hiring clients must establish the proper communication policies and procedures to safeguard workers and prevent incidents.
This article briefly discusses the hazard communication concept and six essential steps for its implementation and execution.
What is Hazard Communication?
“Hazard communication” is a set of procedures companies execute to safeguard employees from hazardous substances that endanger their well-being. These processes are critical for properly handling, processing, or storing chemical products.
In the United States, OSHA’s Hazard Communications Standards stipulate that labels, safety data sheets, and employee communications, including training and information, must follow specific standards. These preventive measures can enhance occupational safety and decrease work-related injuries.
Who is Responsible for Establishing Hazard Communication?
The employer handles ensuring a secure working environment. This includes adherence to 29 CFR 1910.1200 (h), the hazard communication standard (HCS) established by OSHA, and supplying sufficient training to employees about the safe handling of hazardous materials. The company is also responsible for ensuring contractors receive the same training and information.
Before starting any project, however, companies should perform a hazard assessment and appoint a trained and experienced supervisor to oversee tasks, ensuring workers follow all safety precautions.
6. Steps of a Hazard Communication Plan
1. Learn the Standard and Decide Who Manages the Plan
Learning OSHA’s hazard communication standards and understanding how they affect you and your workforce are essential first steps for employers who manage hazardous substances. Otherwise, safety managers cannot find what is necessary to support compliance.
Also critical is assigning suitable personnel to oversee the plan’s management, as developing the program once and never revisiting it will not suffice in an ever-changing work environment. The plan’s manager must perform ongoing reviews and adjust the terms as necessary.
2. Keep Accurate Safety Data Sheets
Safety data sheets (SDS) feature comprehensive information about hazardous materials in work environments. They detail each substance’s physical and health hazards, essential protective measures, and related pertinent details.
Companies use these documents to develop proactive workplace safety policies and training programs about effectively managing chemical hazards and informing employees about potential dangers.
U.S. companies should also take note of OSHA’s updated requirements updates for what must appear on safety data sheets. The new standard incorporates a 16-section format needed in every safety data sheet, which is much more comprehensive than the original requirements.
More specifically, these new requirements include (but are not limited to) the following added sections:
- Information on ingredient composition
- Hazard identification
- Substance identification
- Firefighting measures
- First-aid measures
- Accidental release measures
- Guidelines for handling and storage
- Toxicological information
- Ecological information
- Disposal considerations
- Guidelines for transportation
In addition, OSHA recommends that companies design a HazCom advisor to oversee the upkeep of safety data sheets and collaborate with chemical manufacturers on issuing updated information.
3. Practice Proper Chemical Labeling
Employers must ensure that all containers with hazardous compounds and substances are appropriately labeled. These labels must be legible and clearly displayed to enable workers to identify them quickly.
OSHA outlines six attributes that are integral to all labels:
- Hazard statements
- Product identifiers
- Precautionary statements
- Signal words
- Pictograms
- The responsible party’s contact information, typically the importer or manufacturer
4. Develop a Written Hazard Communication Program
Developing and upholding a written hazard communication program is another critical step in following the OSHA Hazard Communication Standard. This document should include a detailed explanation of how work sites will implement the standards, aiding in coordinating and systematizing the program.
When developing these HazCom blueprints, companies should ensure that the following details are incorporated:
- An inventory of all hazardous materials
- Detailed procedures for labeling them
- Guidelines for managing safety data sheets, as discussed above
With a few exceptions, these requirements are non-negotiable for most employers who handle substances in the workplace.
5. Train all Workers in Hazard Communication
Companies must supply worker training on accessing and utilizing SDSs and label information and all other facets of your HCS program, including but not limited to:
- The available protective measures
- How to implement those measures
- Whom to contact in case of an issue or emergency
OSHA’s HCS requirement also stipulates that companies must provide training in a manner and language suitable for all workers, and they must review the material periodically to ensure retention. This process establishes the training language(s) and how employers conduct it.
A critical (but sometimes ignored) aspect is periodic worker retraining, which should occur for everyone when:
- Onboarding new workers
- Introducing new hazardous substances
- Losing employees who handle a specific material
Although federal OSHA does not mandate periodic training for employees, it is advisable to implement regular exercise as a standardized procedure to aid in the retention of vital HCS information by staff.
6. Evaluate and Revise the Plan
Lastly, the hazard communication program must remain up-to-date and pertinent to everyone in the company, and reviewing and revising the program periodically to account for workplace changes is necessary to carry this out.
Those changes might include the following:
- The introduction of new chemicals
- Newly discovered hazards
- A change in required processes
- Policy updates
- New personnel
By viewing the HCS program as a living, breathing entity instead of a one-time mandate, companies can mitigate the risk of committing severe violations as their situations change.
It also shows workers that management proactively prioritizes their safety, contributing to a more robust safety culture and enhancing the organization’s overall sustainability.
Combine a Hazard Communication Plan with the Industry’s Best Safety Solutions to Protect Your Workforce
Creating and implementing a sound hazard communication plan is crucial to promoting workplace safety by laying out a process for identifying, handling, and disposing dangerous substances.
However, an effective plan alone isn’t enough to maximize worker safety. Companies must also integrate a process safety management solution that offers the chemical training necessary to support safety standards and create a culture of continuous safety improvement.
Consider partnering with us to tailor a solution to your hazard communication plan and protect your workers from the risks of handling dangerous substances.
Contact us today to learn more.