
Top 10 Safety Hazards in Downstream Oil and Gas Operations
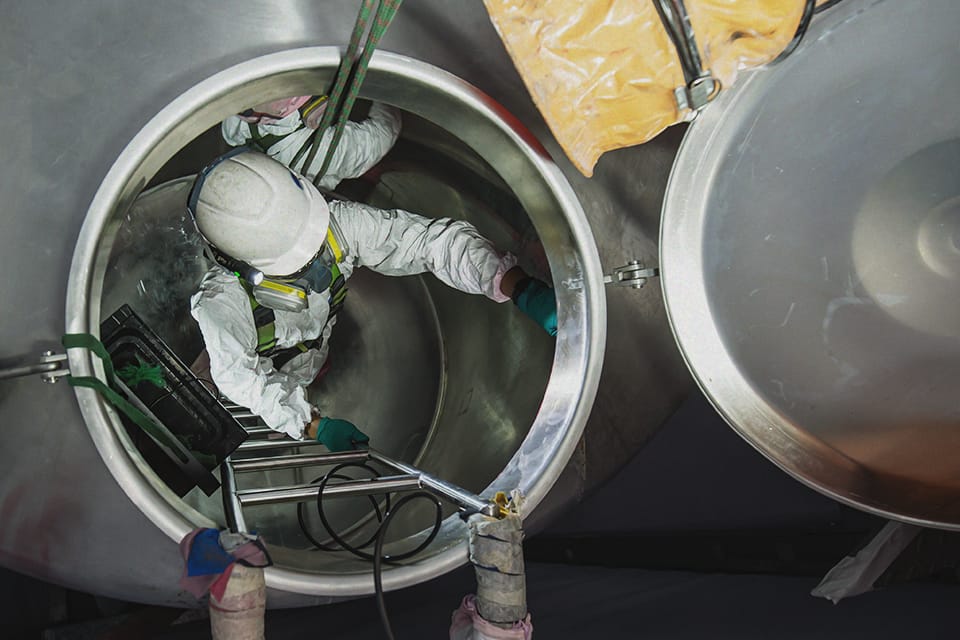
The downstream oil and gas industry keeps the world running by transforming crude oil into fuels that help power other sectors. However, handling these hazardous substances makes safety a top priority in downstream oil and gas operations, where the raw materials are processed into usable oil and gas products. Even with regulations in place, these facilities still present inherent dangers.
Understanding and preventing these dangers is crucial for oil and gas companies and workers in the downstream sector. This article explores the ten most significant safety hazards in downstream oil and gas and offers ways to keep everyone safe on the job.
Top 10 Safety Hazards in Downstream Oil and Gas Operations
1. Explosions and Fires
Downstream facilities handle a lot of flammable liquids and gases, which can quickly explode or catch fire. Many situations can cause sparks that ignite these materials, including the following:
- Welding
- Cutting
- Striking tools together
- Using damaged tools
- Working with dry powders
Additionally, leaks and spills can create pockets of flammable vapor, and equipment failure can lead to uncontrolled releases that could spark an explosion.
To prevent fiery disasters, downstream facilities require permits for any activity that could create sparks near flammable materials, like welding or cutting. These permits ensure proper precautions are taken.
Regular equipment inspections and maintenance are crucial to catch leaks early and ensure proper ventilation to prevent flammable vapor build-up. Additionally, having clear emergency response plans helps everyone know how to respond to fires and explosions, including:
- Using fire extinguishers
- Evacuating safely
- Contacting emergency services
2. Slips, Trips, and Falls
Several factors can result in slips, trips, and falls and lead to severe injuries, including:
- Uneven surfaces
- Wet floors
- Contaminated surfaces
- Cluttered walkways
- Improper footwear
Promptly cleaning up spills and scheduling regular cleaning keep work areas clean and dry, preventing slips and falls. Enforcing good housekeeping practices eliminates clutter and tripping hazards by designating specific areas for storing tools and materials.
Also, providing workers with slip-resistant footwear further minimizes the risk. Training in safe walking techniques around hazards, including uneven surfaces, lifting tasks, and clear communication in busy work zones are all essential.
3. Confined Space Entry
Downstream facilities have many confined spaces, such as the following:
- Storage tanks
- Wessels
- Pits
- Vaults
Entering these spaces can be dangerous because of a lack of oxygen, exposure to toxic fumes, and the risk of getting trapped.
A thorough risk assessment must be done before anyone enters a confined space. This evaluation identifies potential hazards, necessary permits and procedures, and proper ventilation requirements.
The proper permit system for confined space entry sets up many necessary safeguards, such as:
- Detailed entry procedures
- Air monitoring protocols
- Emergency evacuation plans are in place
Adequate ventilation is essential to ensure there’s enough oxygen and no harmful fumes before anyone enters, which might involve using ventilation systems.
Equally as important, always having a “buddy” outside the confined space, checking on the worker inside, and being ready to take action in case of an emergency is another crucial safety measure.
4. Chemical Exposure
Downstream facilities use various hazardous chemicals for processing and cleaning, including the following:
- Sodium hydroxide
- Ethanol
- Corrosion inhibitors
- Sulfuric and hydrochloric acid
Exposure to these chemicals happens by breathing them in, getting them on your skin, or even swallowing them. This can lead to breathing problems, burns, and poisoning.
Chemical safety starts with adequately labeled containers and readily available safety data sheets (SDS) for each on-site chemical. These documents provide crucial information on each chemical’s properties, hazards, and safe handling procedures.
Workers must be trained on the safe handling and storage of chemicals, including how to wear personal protective equipment (PPE), such as:
- Goggles
- Face shields
- Gloves
- Respirators
Additionally, engineering controls like ventilation systems can minimize exposure risks by removing hazardous fumes and vapors at the source, reducing the risk of inhalation.
5. Electrical Hazards
Downstream oil and gas workers rely heavily on electrical equipment, sometimes leading to shock and even electrocution. This could happen for several reasons, including:
- Faulty wiring
- Damaged insulation
- Improper grounding
- Unqualified electrical work
A preventative maintenance program for electrical equipment is crucial for identifying and addressing potential problems before they occur. This program should involve regular inspections by qualified electricians.
Ensuring proper grounding of all electrical circuits and equipment provides a safe path for stray current to flow, preventing it from traveling through a worker’s body in case of a fault.
Equally critical, management must verify that workers are qualified for the job site and ensure they have the proper training in safe work practices, including lockout/tagout procedures.
These procedures ensure that electrical equipment is de-energized and locked out before any maintenance or repairs are undertaken, preventing accidental energization and potential shock hazards.
6. Dropped Objects
Dropped objects, especially from heights, pose a significant safety risk to workers below. Those items include the following:
- Portable tools
- Equipment components like slings and chains
- Pipes and valves
- Metal scraps
The secure storage of tools and equipment during storage and transportation is essential, and designated storage areas with shelving, racks, and cabinets are required to prevent items from falling.
Also, safety teams should establish designated work zones for lifting operations and restrict access to these areas for those below, minimizing the risk of injury from falling objects.
Implementing a proper lifting and rigging program ensures workers are trained on safe lifting procedures. The steps should include the following:
- Pre-lift planning and risk assessment
- Proper lift supervisor and worker training
- Equipment inspection
- Executing safe lifting practices
- Reporting incidents and near misses
7. Machine-Related Injuries
Downstream facilities use a wide range of machinery for processing and packaging. Failure to properly guard these machines can lead to several types of injures, including:
- Lacerations
- Strains and sprains
- Fractures
- Punctures
- Crushing
Ensuring all machinery has proper guards installed and maintained in good working order is paramount. These guards are designed to prevent accidental contact with moving parts of the machinery.
Of course, all workers must be trained on safe operating procedures for specific machines and the importance of never bypassing machine safeguards. They should understand the function of each guard and the potential hazards associated with bypassing them.
Also, management should implement lockout/tagout procedures to prevent accidental equipment startup during maintenance or repairs. These procedures ensure that energy sources are isolated and locked out before any work is undertaken on machinery.
8. Noise Exposure
Downstream facilities often generate significant noise levels from pumps, compressors, and other equipment. Prolonged exposure to loud noise can lead to several ear-related injuries, including:
- Hearing loss
- Tinnitus (ringing or buzzing in the ears)
- Hypertension
- Sleep disturbances
Regular noise monitoring helps identify areas exceeding suitable noise levels, and implementing a hearing conservation program that includes providing workers with appropriate hearing protection, such as earplugs or earmuffs, helps reduce noise exposure and prevent hearing damage.
Also, safety managers should encourage workers to take breaks in quieter areas throughout their shift to minimize noise exposure. Rotational work schedules can also help reduce the cumulative effects of noise exposure.
9. Psychological Stress
The high-pressure environment of downstream operations, potential safety risks, and shift work schedules can contribute to psychological stress for workers. Chronic stress can negatively impact:
- Focus
- Decision-making
- Overall well-being
Fostering a culture of open communication where employees feel comfortable reporting safety concerns and requesting help is key. Training in stress management techniques like mindfulness and relaxation exercises can be extremely valuable.
Also, encouraging employee participation in decision-making promotes a sense of ownership and control, and offering employee assistance programs (EAPs) provides confidential mental health support.
10. Ergonomic Hazards
Downstream facilities often involve workstations or equipment that results workers completing tasks with poor posture, which can result in physical problems such as:
- Headaches
- Back, neck, and shoulder pain
- Osteoarthritis
- Muscle strains
- Tendinitis
Conducting ergonomic assessments of workstations and equipment is crucial to prevent these ailments.
Ideally, workplaces should be designed to fit the worker, minimizing awkward postures and repetitive motions, and providing adjustable workstations and chairs to help accommodate individual needs.
Managing Safety Hazards Requires the Best Process Safety Management System
Keeping workers safe is essential in downstream oil and gas operations. By proactively identifying and mitigating these top 10 hazards, companies can create a safer job site for their workers.
However, providing maximum protection to your workforce requires adding a process safety management solution designed for the downstream oil and gas sector. Consider partnering with us to create a program that promotes safer work environments and reduces on-site incidents.
Contact us today to learn more.