
The Partnership Imperative: Working Together to Improve Contractor Safety Compliance
Leading companies recognize that cultivating an internal safety culture is critical to the long-term success of the business. Many of these proactive businesses are also working to extend that culture across their contractor workforce, too.
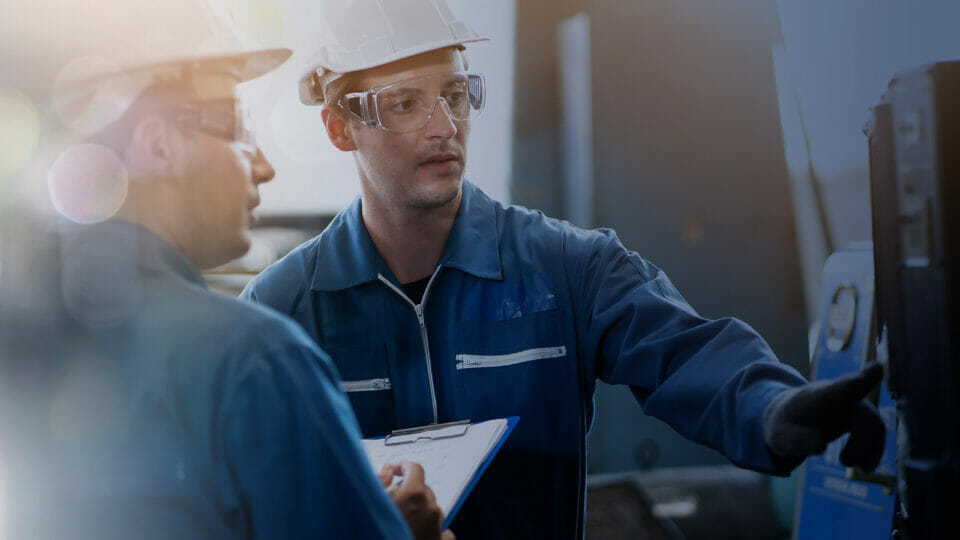
This article was originally published on Occupational Health & Safety’s website. To read the article on OHSonline.com, click here.
You’ve probably heard the saying, “No man is an island.” When it comes to contractor safety compliance, the saying should be, “No company is an island.”
Leading companies recognize that cultivating an internal safety culture is critical to the long-term success of the business. Many of these proactive businesses are also working to extend that culture across their contractor workforce, too.
These companies have recognized the value of implementing a contractor safety compliance program that helps prevent worker injuries, protect the company’s reputation, minimize operational disruption, support compliance with government regulations, and avoid potential fines and unnecessary loss.
To say that lax safety compliance among your contractors invites trouble is an understatement. Just look to the example of Tesla, which is currently under investigation by the state of California for multiple worker injuries on its automobile assembly line. While Tesla has tried to distance itself by arguing that a subcontractor is responsible, it’s Tesla’s brand and reputation that are suffering due to the bad press, not the contractor’s. Or the impact to Ford, which had to halt production of its best-selling F-150 truck for two weeks in May when one of its parts suppliers, which had a history of safety violations, suffered an explosion that injured two workers and took its plant offline. Ford has stated it expects the temporary halt in F-150 production resulting from its contractor’s safety incident to have an adverse effect on its second quarter earnings.
These examples abound, highlighting the critical importance of establishing a contractor safety program that ensures your safety standards are well-defined and consistently applied across all your contractors through a prequalification and monitoring process that evaluates contractor compliance with OSHA and company-specific safety requirements.
The Business Case for Partnership
A formal contractor safety compliance program benefits both your company and your contractors in a number of ways. First, it ensures all of your contractors clearly understand your particular standards and expectations when it comes to safety. Next, it demonstrates your desire to partner with the contractor to support safe workplaces.
It may be simpler to run a program that takes the tone of “submit your program information and if it’s not good enough we won’t do business with you.” However, such a program doesn’t help your company attract contractors as long-term business partners and doesn’t help your contractors know where they’re going wrong, so they can correct any safety issues. It also doesn’t acknowledge the business reality that sometimes, due to the specialized nature of the work performed or its location, your contractor options are extremely limited, making it difficult to draw such a hard line.
Rather than taking a punitive approach, you can make safety compliance a win-win for everyone involved. To do this, your company will need to provide its contractors with a framework to measure their program’s performance and tools and resources for program improvement should any safety gaps be identified. This helps your company build more profitable, mutually-beneficial partnerships with your contractors.
Whether your company chooses to manage your contractor safety compliance program in-house or with the help of a third-party vendor, it pays off when your business takes a partnership approach to maintaining safety on your work sites.
Building a Compliance Partnership
You know that ideally a contractor safety compliance program helps your company streamline contractor safety prequalification processes, accelerate contractor time-to-work, and gain insight into contractor safety program quality and trends.
How do you know if your current program supports the partnership approach you want when hiring and working with contractors? Two critical, but often overlooked, ways to move your contractor safety compliance program toward a partnership model are a detailed grading system and a formal audit process with corrective action follow up.
Here’s what those look like:
1. A meaningful grading system
It’s not uncommon for companies to use a simple “approved” versus “unapproved” status for their contractors, based on a review of information they’ve gathered during the prequalification process about a contractor’s safety program and track record. While this is a solid starting point, a more strategic contractor safety compliance program will apply a scoring model to a contractor’s prequalification data and rate the contractor’s safety program in the form of a letter grade A through F.
The advantages of this more exacting grading system over a vague “stamp of approval” are myriad.
For safety professionals, a letter grade arms you with another data point to measure a contractor’s improvements over time and assess whether they are like-minded about the importance of safety and taking the initiative to get better. A static “approved” status can’t tell this story in the same way as a C grade that, over time, becomes an A.
Letter grades also offer a useful barometer when you need to choose between spending your time performing observations and audits on your C or B contractors versus your A contractors.
For in-office or field team members who hire contractors, a letter grading system gives your team better information as they make hiring choices. After all, don’t you want to hire A contractors over C contractors whenever possible? Jobs run more smoothly when your managers are able to focus on project details, rather than worrying about whether basic safe work practices are being deployed by a contractor.
Plus, safety and quality typically go hand in hand, so hiring A contractors whenever possible helps you deliver higher-quality results for the business, and that’s good for the bottom line.
In those scenarios where your contractor options are limited, knowing that you’ll be relying on a C contractor enables you to proactively put an appropriate mitigation plan in place – for example, do you require one of your own safety professionals on-site to provide oversight during the project?
Ultimately, employing letter grades as part of your contractor safety compliance program is a simple, yet effective way for hiring companies to monitor and encourage safety improvement, guide decision-making, and focus investment of safety resources.
2. Audits and corrective actions
If you’ve not yet introduced contractor safety audits into your program, here’s your chance to make dramatic improvements in safety compliance and provide tools to help drive the C contractors that are critical to your operations closer to an A.
Audits provide invaluable verification that the safety program and policies a contractor reports having in place during your prequalification process are, in fact, being successfully put into action. This can be especially important when you employ contractors to perform higher-risk activities on your behalf.
Audit results provide you with additional data and deeper intelligence regarding the quality of a contractor’s safety program. Does the contractor have records that demonstrate they’re actually conducting required training, inspecting equipment, performing JHAs, etc.? Such information helps inform hiring decisions and target safety efforts and resources – for example, where to perform contractor safety observations and what to look for during those inspections.
However, to truly partner with your contractors and help them drive long-term safety improvements, your audit program must include providing specific recommendations for corrective actions when program gaps are identified. Then, most critically, there should be a follow-up audit conducted that allows you to verify whether recommended program upgrades were, indeed, made.
This process helps drive ongoing safety improvement that can be measured through improvement in audit scores and overall safety letter grades over time, as well as statistics like TRCR (total recordable case rate) and EMR (experience modifier rate). It’s also where the rubber meets the road in terms of evaluating a contractor’s true commitment to your partnership. If there’s inaction when provided a specific list of corrective actions needed, it’s likely time to part ways.
Bringing Method to the Madness
Done right, managing contractor safety compliance programs in-house can require a significant investment of time to track down and review contractors’ safety data and documents and perform initial and follow-up contractor audits.
A third-party partner can take on these time-consuming tasks and partner with you and your contractors to streamline the safety prequalification process and improve contractor safety compliance, freeing internal staff to spend their time on higher-value activities. However, it’s essential any third-party vendor you employ shares your partnership approach to contractor safety compliance.
You want to ensure a vendor’s software has the flexibility and configurability to calculate and display a safety letter grade based on your company’s unique requirements.
Third-party audit services can be an excellent way to gain more eyes in the field when internal resources are limited, as well as the valuable perspective of auditors who’ve worked with a variety of clients and industries. But, for maximum safety improvement impact, be certain the vendor’s contractor audit program includes a corrective actions component that’s reinforced by a follow-up audit.
In short, we all want safer work sites. It’s good for our workers, our clients, and our businesses. By looking at safety programs as a partnership among the hiring company, its contractors, and even its third-party safety compliance vendor, we can improve safety for everyone. Everyone wins if we build partnerships to improve safety, mitigate business risks, and achieve higher-quality results.
Sign up for the latest company updates, knowledge center resources, and more, delivered right to your inbox.
Sign Up for the Latest Updates