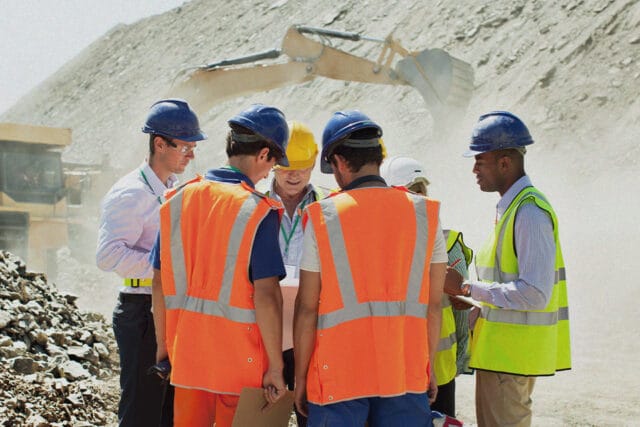
The Human Element in Process Safety: Why Organizational Culture Matters
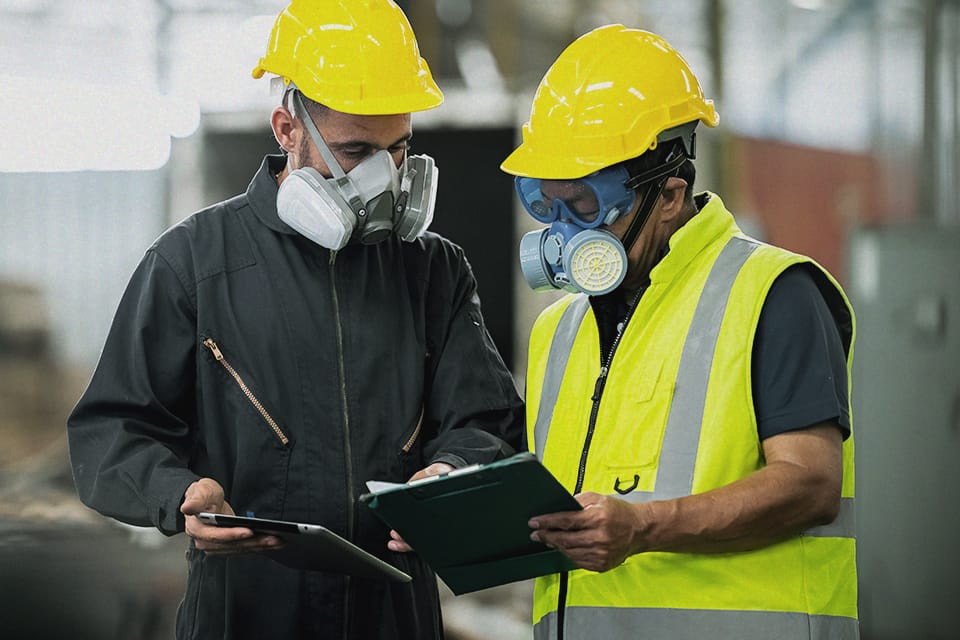
In the dynamic field of process safety management (PSM), understanding the human element is critical for the safe and efficient operation of facilities dealing with hazardous materials. While technological advancements and regulatory compliance play essential roles in ensuring safety, the human factor is often the most influential.
Organizational culture, which encompasses the collective values, beliefs, and behaviors of employees, greatly impacts how safety is perceived and enacted within an organization. Therefore, fostering a robust safety culture is paramount for preventing incidents, encouraging employee participation, and cultivating a safety-conscious mindset.
Understanding Organizational Culture in Process Safety
Organizational culture refers to the underlying beliefs and behaviors that shape how an organization’s members interact and work together. This culture is reflected in the organization’s policies, practices, and work environment. In the context of process safety, a positive safety culture can significantly contribute to effective safety management.
Components of Organizational Culture
- Values: These are the fundamental beliefs that drive decision-making and behavior within the organization. Safety values emphasize maintaining a safe work environment and ensuring all individuals uphold safety standards.
- Norms and Practices: Norms dictate acceptable behaviors within the organization, shaping how people conduct themselves in various situations. Strong safety norms lead to proactive measures, while a lack of norms may result in negligence and complacency.
- Symbols and Language: The use of specific terminology and symbols related to safety reinforces the organization’s commitment to process safety. Creating a common language helps all employees understand and communicate potential hazards effectively.
- Leadership Commitment: Leaders play a pivotal role in shaping the organizational culture. By demonstrating visible commitment to safety initiatives and engaging in regular safety discussions, leaders can encourage employees to adopt a safety-oriented mindset.
The Role of Human Factors in Process Safety
Human factors are the psychological, social, and organizational influences on human behavior in relation to safety. Understanding these factors is crucial for developing effective safety strategies within organizations.
Human Behavior and Its Impact on Process Safety
- Decision-Making Under Pressure: Employees often find themselves in high-pressure situations where quick decisions are necessary. Under stress, cognitive biases and decision-making errors can occur, leading to safety breaches. Organizations should implement structured decision-making processes, such as checklists and standardized procedures, to mitigate errors.
- Risk Perception: Employees perceive risk differently based on personal experiences, training, and organizational messaging. Accurate risk perception influences safety behavior. Organizations can enhance risk perception through regular training that emphasizes recognizing and addressing potential hazards.
- Communication Patterns: Open communication is vital in cultivating a culture of process safety. Barriers to effective communication can lead to misunderstandings and misinformed safety practices. Training employees on how to escalate safety concerns and participate in safety discussions can improve communication channels and transparency.
- Behavioral Safety Initiatives: Encouraging safe behaviors while discouraging unsafe practices is essential. Recognizing that unsafe behaviors can stem from systemic issues helps organizations develop effective behavioral safety initiatives. Rewarding safe behavior and providing real-time feedback can foster a safety mindset.
The Importance of a Safety-Conscious Mindset
A safety-conscious mindset involves individual and collective accountability regarding safety practices. Cultivating this mindset begins with instilling the belief that every employee plays an integral role in maintaining a safe working environment.
Key Elements of a Safety-Conscious Mindset
- Awareness of Risks: Employees must be trained to identify potential hazards and remain vigilant. Regular risk assessments and safety drills reinforce this awareness.
- Personal Responsibility for Safety: A culture that encourages accountability fosters an environment where employees take responsibility for their safety and their colleagues’. Clear roles and expectations related to process safety promote a sense of duty.
- Continuous Improvement: Safety culture must evolve through regular feedback, audits, and engagement. Organizations prioritizing continuous improvement encourage employees to share insights, suggest safety enhancements, and learn from past incidents.
- Recognition of Safe Practices: Recognizing employees who consistently adhere to safety protocols enhances motivation and compliance. Reward systems, such as employee of the month programs or public acknowledgment of safety contributions, reinforce a culture of safety.
Employee Participation in Process Safety Initiatives
Active employee participation is vital for a robust safety culture. When employees engage in safety initiatives and contribute ideas, they take greater ownership of safety practices.
Ways to Enhance Employee Participation
- Involvement in Safety Committees: Forming safety committees with employees from various roles facilitates collaboration and innovation in process safety practices.
- Feedback Mechanisms: Establishing clear feedback channels for employees to voice concerns and suggestions regarding safety practices encourages a culture where suggestions lead to positive changes.
- Utilizing Incident Reporting Systems: Encouraging employees to report near-misses and incidents without fear of punishment provides significant insights into potential safety hazards. A ‘just culture’ ensures accountability without penalizing honest mistakes.
- Safety Training and Workshops: Interactive training sessions and workshops engage employees in process safety material. Real-life case studies and simulations offer hands-on learning experiences.
- Safety Walks and Inspections: Organizing safety walks or joint inspections with leadership encourages participation and demonstrates management’s commitment to safety.
The Benefits of Organizational Safety Culture Surveys
Conducting organizational safety culture surveys is a valuable tool for assessing the current state of safety within an organization. These surveys provide insights into both overt and covert attitudes and practices surrounding process safety.
Advantages of Safety Culture Surveys
- Identifying Strengths and Weaknesses: Safety culture surveys help organizations discern areas of excellence and areas requiring improvement.
- Benchmarking: Comparing survey results against industry standards or similar organizations helps identify gaps and opportunities for improvement.
- Engagement and Ownership: Involving employees in the survey process increases engagement. Promoting transparency about findings and actions enhances trust.
- Setting Measurable Goals: Surveys provide a quantitative measure of safety culture, guiding strategic planning and supporting safety improvement initiatives.
- Continuity Over Time: Regular surveys allow organizations to track progress, highlighting improvements or deteriorations in process safety culture.
Challenges in Cultivating a Process Safety Culture
Organizations may face several challenges when striving for a strong safety culture:
- Resistance to Change: Employees accustomed to existing structures may resist new safety practices. Educational programs highlighting the benefits of process safety help overcome resistance.
- Cultural Differences: In global organizations, diverse cultural backgrounds influence safety attitudes. Tailoring communication and training fosters a unified safety commitment.
- Management Commitment: A lack of leadership commitment undermines safety culture. Leaders must model desired behaviors and prioritize safety in decision-making.
- Resource Allocation: Adequate resources—including training, technology, and personnel—are necessary for improving safety culture. Investing in process safety is essential for long-term success.
Conclusion
In summary, the human element in process safety management is essential for fostering a culture that prioritizes safety. Understanding the role of organizational culture, human factors, and employee participation is paramount for creating a robust safety-conscious mindset. Organizations that actively engage employees, seek feedback through safety culture surveys, and commit to continuous improvement cultivate a positive safety culture at every level.
As industries evolve and safety challenges grow, prioritizing the human aspect of safety is fundamental for mitigating risks and preventing incidents. By embracing a holistic approach that nurtures both organizational culture and individual accountability, companies enhance their safety practices and protect employees. Ultimately, in a world where stakes are high, process safety must be an organizational imperative that defines success and integrity.
About the Author
James A. Junkin, MS, CSP, MSP, SMS, ASP, CSHO is the chief executive officer of Mariner-Gulf Consulting & Services, LLC and the chair of the Veriforce Strategic Advisory Board and the past chair of Professional Safety journal’s editorial review board. James is a member of the Advisory Board for the National Association of Safety Professionals (NASP). He is Columbia Southern University’s 2022 Safety Professional of the Year (Runner Up), a 2023 recipient of the National Association of Environmental Management’s (NAEM) 30 over 30 Award for excellence in the practice of occupational safety and health and sustainability, and the American Society of Safety Professionals (ASSP) 2024 Safety Professional of the Year for Training and Communications, and the recipient of the ASSP 2023-2024 Charles V. Culberson award. He is a much sought after master trainer, keynote speaker, podcaster of The Risk Matrix, and author of numerous articles concerning occupational safety and health.