
What are Ergonomic Hazards? 5 Types and How to Avoid Them
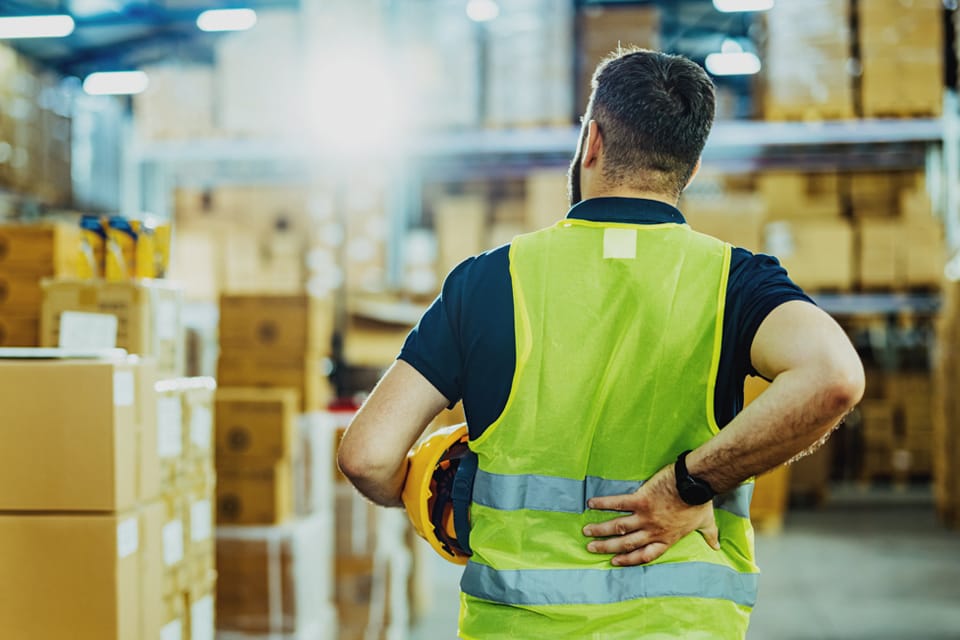
Job sites often expose workers to conditions demanding hard labor and potentially severe physical risks. However, each of those potential dangers, also known as ergonomic hazards, is different. Companies overseeing these sites must implement processes to address those risks specific to their own worksites to safeguard workers from strain, injuries, and weariness.
This article briefly defines an ergonomic hazard, lists five examples, and offers steps companies might take to avoid one.
What are Ergonomic Hazards?
An ergonomic hazard refers to any physical factor in the workplace that could potentially harm your musculoskeletal system, the network of muscles, tendons, and bones. This can include awkward postures, repetitive motions, or forceful exertions. Over time, these hazards can lead to pain, discomfort, and even serious injuries.
5 Common Ergonomic Hazards and How to Prevent Them
1. Excessive Noise
Prolonged exposure to high noise levels can lead to hearing loss and other adverse health effects. To prevent any ergonomic hazard associated with long noise exposure, safety teams should take the following steps:
- Provide hearing protection. Workers should wear proper hearing protection on loud job sites, such as earplugs or earmuffs. Management should ensure the protection devices fit correctly and meet the necessary ratings for the site’s noise levels.
- Select low-noise equipment. Safety teams should choose equipment and machinery with lower noise emissions whenever possible. Manufacturers often supply noise ratings for their products, helping management make informed decisions.
- Create engineering controls. Management should implement engineering controls to reduce noise levels in the workplace, including isolating noisy machinery, using sound barriers or enclosures, or installing vibration isolators.
- Monitor Noise Levels. Management should regularly measure noise levels in the workplace to identify areas with high noise exposure, allowing for targeted interventions.
2. Prolonged Exposure to Vibration Tools or Equipment
Prolonged exposure to vibrating tools and equipment is an ergonomic hazard that can lead to various health issues, including Hand-Arm Vibration Syndrome (HAVS) and Whole-Body Vibration (WBV) effects.
Management can help workers avoid this danger by encouraging them to follow the following guidelines:
- Use anti-vibration tools. Workers should choose tools and equipment designed with built-in anti-vibration features whenever possible. These can help reduce the transmission of vibrations to your hands and body.
- Conduct regular maintenance. Companies should ensure that all tools and equipment are adequately kept. Regularly inspect and repair worn or damaged components that could increase vibration levels.
- Limit exposure time. Management should encourage workers to limit exposure to vibrating tools and equipment whenever possible. Rotate tasks or schedule breaks to reduce continuous exposure.
- Provide the proper personal protective equipment (PPE). Companies should provide the correct PPE, such as anti-vibration gloves, to help reduce the impact of vibration on their hands.
3. The Ergonomic Hazard of Repetitive Motion
Repetitive motion hazards, repetitive strain injuries (RSIs), or musculoskeletal disorders (MSDs) can occur when workers often repeat movements. To avoid the dangers of this ergonomic hazard, companies should consider the following strategies:
- Provide frequent breaks. Companies should insist workers rest and take time to stretch regularly. Short, frequent breaks can help reduce the impact of repetitive motions on your body. Consider offering workers tools or apps that remind them to take breaks.
- Organize and prioritize tasks. Management should encourage workers to plan tasks to minimize the amount of repetitive work required. This strategy might include prioritizing tasks to tackle the most demanding or repetitive ones earlier in the day when workers are rested.
- Encourage workers to alternate tasks. Workers should switch between different tasks or activities to vary their movements, helping prevent the overuse of specific muscle groups.
- Ensure workers rotate jobs. Management should encourage job rotation among workers, allowing them to switch between tasks or positions and reducing the strain associated with repetitive motions.
4. Improper Lifting Techniques
Avoiding the ergonomic hazards of improper lifting techniques is essential for preventing back injuries and other musculoskeletal problems. Whether lifting heavy objects at work or performing everyday tasks, following proper lifting techniques can help protect every worker’s body.
Here are some steps companies should encourage workers to take to avoid these hazards:
- Assess the load. Workers should assess the object’s weight and size before lifting. Make sure you can safely handle it on your own.
- Use proper footing. Furthermore, they should stand with their feet shoulder-width apart to maintain balance. Keep one foot slightly in front of the other for stability.
- Bend at the knees, not at the waist. Workers should squat down to lift by bending their hips and knees, not their waist. They should keep their back straight and support the natural curve of their spine.
- Use mechanical help. Workers should use a dolly, cart, forklift, or another mechanical aid if the object is too heavy or awkward to lift.
5. Extreme Temperatures
Avoiding the ergonomic hazards of extreme temperatures on a job site is essential for the safety and well-being of workers. Here are some strategies to help workers mitigate these risks:
- Implement a heat/cold safety program. Companies can develop and implement a comprehensive heat or cold safety program tailored to the specific environmental conditions of their job site. This program should include guidelines, policies, and procedures for working in extreme temperatures.
- Monitor weather conditions. Management should stay informed about weather forecasts and heat/cold advisories. They can then adjust work schedules and plans to avoid extreme conditions.
- Encourage hydration. Companies should emphasize the importance of staying hydrated, supply access to clean drinking water, and encourage workers to drink regularly, even if they don’t feel thirsty.
- Again, provide the proper PPE. Management should ensure that workers are provided with and wear suitable clothing and PPE for extreme temperatures.
Preventing Every Ergonomic Hazard Requires the Best Risk Management Solutions
Understanding and preventing ergonomic hazards is critical to running a safe and successful job site. However, doing so effectively requires integrating the industry’s premier safety program that enables you to monitor worker compliance, including making sure they complete the training necessary to avoid everyday dangers.
Consider working with us to configure a solution that helps you safeguard workers from the various hazards inherent on job sites.
Contact us today to learn more.