
Safety Metrics: Leading vs. Lagging Indicators
Safety leading indicators are proactive measures that quantify prevention efforts and can be observed and recorded before an injury happens. Whereas lagging indicators are reactive; they only track negative outcomes, like noting an injury once it’s happened.
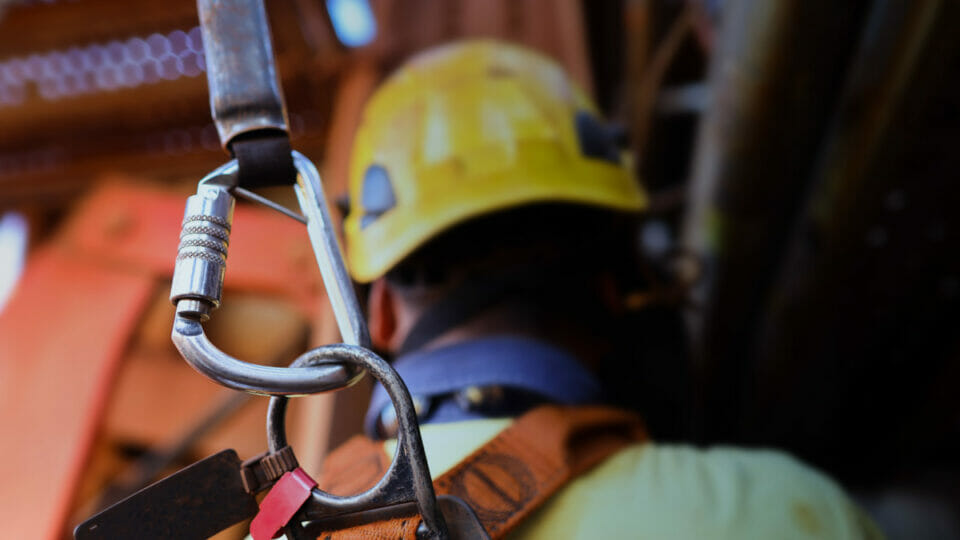
Are you working hard to meet environmental, social, and governance (ESG) requirements? You’re not alone.
The question is: How can you do it well?
The answer is: By collecting and analyzing leading and lagging indicator metrics.
Historically, safety professionals have tracked lagging indicators as is required by law. But employing both leading and lagging indicators will improve safety performance and demonstrate ESG compliance.
Consider this analogy: Imagine your safety performance is a car. Leading indicators look forward through the windshield at the road ahead; lagging indicators look backward through the rear window at the road you’ve already traveled.
Safety leading indicators are proactive measures that quantify prevention efforts and can be observed and recorded before an injury happens. Whereas lagging indicators are reactive; they only track negative outcomes, like noting an injury once it’s happened.
Understanding these and other differences — and ensuring both metrics are in place — will protect your team and help you build an accurate understanding of ESG performance.
Get to know leading indicators
The Occupational Safety and Health Administration (OSHA) defines leading indicators as “proactive, preventive, and predictive measures that provide information about the effective performance of your health and safety activities.” One example is the amount of time taken to respond to a safety hazard report. Quicker response times indicate that management is aware of and committed to improving workplace safety.
In this way, leading indicators focus on quantifying positive measures to ensure safety compliance and can tell you whether your safety and health activities are effective at preventing incidents. They focus on proactive and preventative measures that can help workers avoid accidents while strengthening other safety and health outcomes in the workplace in the process. This includes addressing issues that precede injuries, illnesses and other safety incidents that could cause potential problems with your safety procedures.
Although there are numerous leading indicators that can be collected, it’s easiest to categorize them by specific functionality. This includes:
- Observation-based indicators assess a specific instance of behavior or condition to determine the risk of injury. This includes safe observations, unsafe observations, and participation.
- Operations-based indicators relate to the function of an organization’s infrastructure. Examples include schedule/productivity influences, risk assessments, risk mitigation through improved hierarchy of control, preventive maintenance, training efforts, and timely closure of open safety issues.
- System-based indicators relate to the management of a safety system, including management commitment efforts, psychosocial aspects, culture, and design.
These leading indicators for workplace safety can be tracked to meet your business’ ESG commitments and requirements. Track them against the “S” for social responsibility in your ESG initiatives using a compliance tracking system like Veriforce to collect ESG data.
Here are 4 advantages of measuring leading indicators that can benefit both workers and employers:
- Thwart fatalities, injuries and illnesses in occupational settings. Taking action before occurrences happen makes workers feel valued and boosts productivity.
- Reduce costs associated with adverse events, increasing profitability in the process. Identifying and repairing safety hazards before an incident occurs reduces repair costs, production costs, workers compensation costs, and legal and regulatory expenses typically tied to safety incidents.
- Improve safety and health performance. Monitoring leading indicators related to safety and health performance allows you to strengthen performance in key areas such as management leadership, worker participation, education and training, and program evaluation and improvement.
- Increase worker participation in safety initiatives. Workers who are educated, informed, and willing to adhere to safety protocols feel safer. This helps management learn how engaged their team is and provides actionable information needed to avert potential safety issues.
Get to know lagging indicators
Lagging indicators are the opposite of leading indicators, and focus on safety incidents that happened in the past.
Highlighting existing failures in a company’s safety program allows organizations to make positive changes instead of allowing known hazards to continue to be the cause of accidents. It also measures the effectiveness of existing safety measures.
Here are some examples of lagging indicators:
- The number or location of OSHA recordable incidents
- Incident rates including the total recordable incident rate (TRIR), days away/restricted/transfer rate (DART), and lost time incident rates (LTIR)
One Bureau of Labor Statistics (BLS) is a great example of a lagging indicator — OSHA 300 logs. Private industry employers reported 2.7 million nonfatal workplace injuries and illnesses in 2020, a decrease of 5.7% from the previous year.
A good safety program should not rely solely on lagging indicators because, by definition, they’re reactive. While it’s necessary to track lagging indicators, they provide little direction or insight to the behaviors and conditions that precede incidents.
Be proactive, rather than reactive
To be clear, leading and lagging indicators are both essential for a robust safety program, but leading indicators should play a larger role as they work to prevent accidents rather than highlighting changes that need to be made after an incident occurs.