
Process Safety Management in Manufacturing: A Primer
Process Safety Management requires leadership across all functional elements of departments at manufacturing facilities.
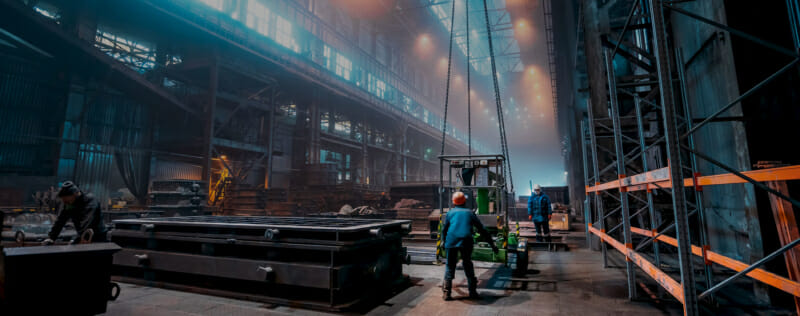
Process safety focuses on preventing fires, explosions, and chemical accidents in chemical process facilities or other facilities dealing with hazardous materials, such as refineries and oil and gas (onshore and offshore) production installations. However, many manufacturing facilities also store and process hazardous chemicals that fall under the Occupational Health and Safety Administration (OSHA) Process Safety Management (PSM) regulations (1910.19).
What Determines a Process Safety Management Facility?
PSM applies to:
- Processes that involve regulatory-based threshold quantities of chemicals listed in the Appendix A of 1910.19;
- Processes where there are 10,000 lbs. or more of a Category I flammable gas (per 1910.1200(c)) or flammable liquids with a flashpoint below 100 degrees on site in one location; and
- Manufacturing explosives or pyrotechnics in any quantity.
Some examples of highly hazardous chemicals that fall under PSM are as follows:
- Anhydrous ammonia (industrial refrigeration and ice skating rinks)
- Chlorine (water treatment systems and biocide companies)
- Several types of acids (laboratories and pharmaceutical companies) Phosphorous compounds (fertilizer and pyrotechnics manufacturers)
- Hydrogen sulfide (a byproduct of organic matter breakdown)
The PSM standard lists 137 hazardous chemicals and threshold quantities (TQ) above which employers must develop and implement PSM programs.
Touchpoints for Process Safety Management in a Manufacturing Facility
The three main touchpoints involved in PSM in any manufacturing facility are:
- process (systems and risk process),
- people (including training and competency, human factors, leadership, and culture), and
- plant (continuously improving plant safety, layers of protection, design, operating limits, etc.).
Process aspects of PSM should be under the strict control of process safety personnel having specialized engineering capabilities. Review, application, and auditing of the process and management of the people involved in a PSM situation are frequently under the control of the plant’s occupational health and safety personnel.
Safety professionals should possess or acquire process safety knowledge and the capability to develop sound process safety information (e.g. operations and maintenance procedures, process and instrumentation diagrams and schematics, hazardous area dossiers, process safety critical equipment, barriers, and performance standards) with the assistance of the specialized process safety engineers.
There are similarities and overlaps between the PSM and occupational health and safety roles for the safety professional. The management of process safety within the organization needs leadership across all functional elements of departments, including the following:
- Knowledge of competence of personnel
- Engineering and design understanding
- Equipment and process information
- Strict systems and procedures for safe work
- Audit and assurance guidelines
- Management of human factors and culture
- A robust training program
What is a Process Safety Management “Event”?
A PSM incident is the unexpected release of toxic, reactive, or flammable liquids and gases in highly hazardous chemical processes. More specifically, a PSM event results from a process directly involved in the damage caused. This includes equipment, technology on and off-site, release or reaction from the highly hazardous chemical, and any appurtenances such as reactors, tanks, and piping.
A PSM incident is when a pipeline or processing facility has a mechanical failure, which can cause a fire, explosion, rupture, or chemical leak. The following short summaries illustrate some infamous PSM events in recent history. These unfortunate examples demonstrate that industrial processes can have devastating consequences for employees, the public, and the environment without proper process safety management; even further highlighting the need for companies to implement PSM programs.
Bhopal Disaster in 1984
A chemical leak at a US-Owned Union Carbide pesticide plant based in India resulted in the deaths of over 3,000 people and injuries to hundreds of thousands more. The incident highlighted the importance of proper PSM, as the company did not maintain the plant properly or follow safety procedures.
Texas City Refinery Explosion in 2005
A series of explosions at the Texas City Refinery in Texas resulted in the deaths of 15 workers and injuries to 170 others. The incident resulted from a failure to maintain equipment and a lack of adequate safety procedures correctly.
Deepwater Horizon Oil Spill in 2010
The Deepwater Horizon spill resulted from a blowout at an offshore oil rig. The incident killed 11 workers and caused significant and long-lasting environmental damage to the spill area’s shores, wildlife, and ocean. The investigation found that the blowout resulted from a failure to properly manage the risks associated with the drilling process.
These events are just a small sample of dozens of the PSM incidents each year.
Getting Started (or Getting Up to Speed)
OSHA Process Safety Management requires that employers covered by the PSM standard in manufacturing implement safety programs that identify, evaluate, and control these hazards, similar to the safety programs that are found in a refinery or oil and gas industry situation.
What many safety professionals may find complex or confusing when reviewing or creating a PSM safety program is that the OSHA PSM standard is “performance-based,” which means that the standard outlines critical features of safety programs for controlling highly hazardous chemicals, but employers have the flexibility to put together their safety programs to the unique conditions at their facilities. If this seems daunting, it is time to call an expert to help you discover the best way to comply.
Specifically, there are fourteen regulatory requirements of the standard, or “process safety elements”:
- Contractors
- Employee Participation
- Pre-startup Safety Review
- Process Safety Information
- Process Hazard Analysis
- Operating Procedures
- Training
- Mechanical Integrity
- Compliance Audits
- Emergency Planning and Response
- Trade Secrets
- Hot Work Permit
- Management of Change
- Incident Investigation
Who Needs Process Safety Management in Manufacturing?
Chemical Manufacturing
The chemical manufacturing industry stores, processes, mixes, stores, and transports large quantities of highly hazardous chemicals. These manufacturers are obligated to prevent incidents such as explosions or chemical releases that can cause harm to employees and the surrounding community.
Pharmaceutical Manufacturing
In the pharmaceutical industry, process safety management is critical to ensure that the drugs produced are safe for human consumption and that the manufacturing process complies with regulatory guidelines.
Oil and Gas Industry
It is essential to prevent incidents such as oil spills or gas leaks, which can have a significant environmental impact and loss of life due to not following and auditing sound PSM design, procedures, and policies.
Food and Beverage Industry
In the food and beverage industry, process safety management helps prevent food-borne illnesses and ensure food is safe for consumption. In addition, industrial refrigeration is associated with the storage and management of large amounts of anhydrous ammonia.
Power Generation
It’s vital to prevent power plant incidents like explosions or fires that can harm people and the community. Managing the quantities of fuel and chemicals used in power generation is a crucial task.
Process Safety Management in Manufacturing is Critical
Process Safety Management isn’t just for the oil and gas industry. Many manufacturing facilities in different industries fall under the PSM standard and require compliance with the 14 prescriptive elements of the PSM standard.