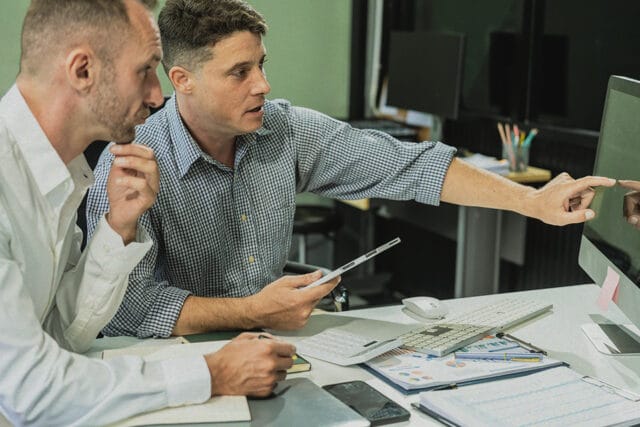
Digital Solutions That Help Food Manufacturers Optimize Contractor Management
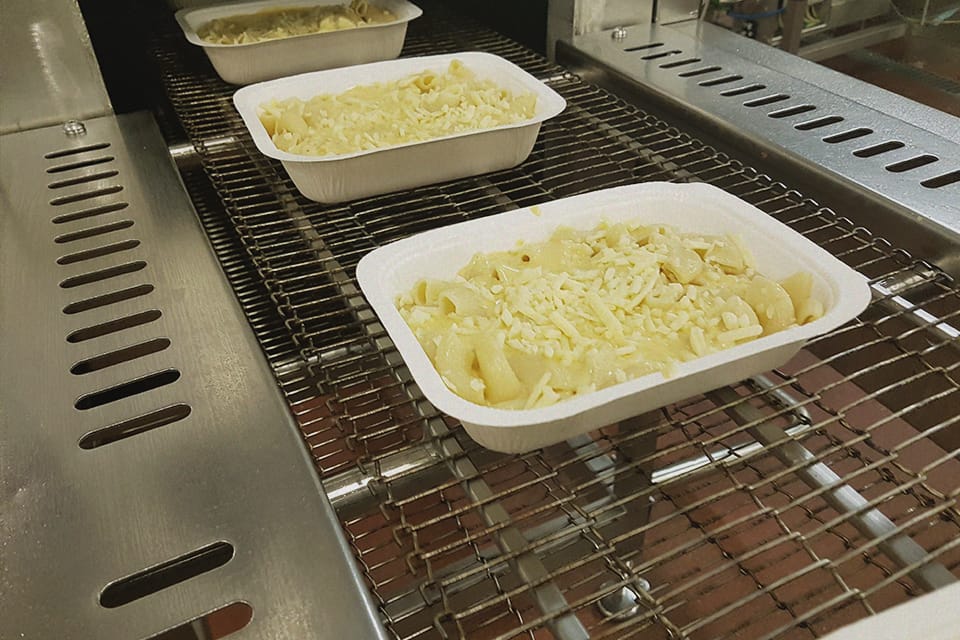
In the fast-paced, highly regulated, and increasingly globalized food manufacturing industry, food manufacturers must prioritize strict health, safety, and environmental (HSE) practices.
Given the complexities of maintaining food safety, quality, and regulatory compliance, food manufacturers often rely on contractors for specialized services. These include construction, facility management, maintenance, logistics, IT support, food product development, and security. However, ensuring contractor safety, performance, and compliance is a major challenge.
Traditionally, HSE teams have relied on manual checks, paperwork, spreadsheets, and post-incident reports to track contractor activities. Today, digital solutions are transforming contractor management by boosting efficiency, enhancing oversight, and enabling real-time safety monitoring.
The Digital Transformation of Contractor Safety and Compliance
Digital technology is changing how food manufacturers manage contractor safety and compliance. Cloud-based tools, AI analytics, and IoT sensors make safety protocols easier to enforce in real time.
1. Real-Time Monitoring with IoT
IoT sensors embedded in tools, PPE, or equipment continuously monitor temperature, humidity, air quality, and contractor behavior. These devices generate data and trigger alerts if safety thresholds are breached, prompting immediate action. In food manufacturing, this helps maintain hygiene, manage hazardous materials, and monitor equipment maintenance.
2. Predictive Analytics for Risk Reduction
AI-powered analytics can predict safety risks by analyzing historical data. These tools identify patterns and forecast issues before they occur. For instance, AI can flag machinery needing maintenance or alert HSE teams to potential audit failures. As a result, food manufacturers can act proactively.
3. Streamlined Contractor Onboarding
Digital tools like Veriforce Worker Pass (VWP) ensure contractors meet safety and compliance standards before entering the site. Certifications, insurance, and training are verified through one platform. These tools also track ongoing contractor performance, helping HSE teams maintain a culture of compliance.
4. Efficient Incident Reporting
Digital platforms make it easier for contractors and HSE staff to report safety hazards and near-misses immediately. Automated routing and root cause analysis accelerate corrective actions. Compared to paper-based systems, these platforms improve reporting accuracy and responsiveness.
5. Remote Training and Knowledge Access
Platforms like VWP host compliance documents and training modules. Contractors can complete safety courses remotely, staying updated on evolving regulations. This improves training consistency, lowers risks, and reinforces food safety standards.
Why Food Manufacturers Face Challenges with Digital Integration
Despite clear advantages, integrating digital solutions into existing systems can be difficult. HSE teams must overcome several barriers to achieve full adoption.
1. Resistance to Change
Some employees and smaller contractors prefer traditional practices, including paper checklists and face-to-face communication. These users may find digital platforms complicated or unfamiliar. Effective change management—including training, support, and communication—is essential to ease the transition.
2. System Compatibility and Data Integration
Legacy systems can be difficult to integrate with new digital platforms. Often, data is scattered across separate tools for training, equipment, and compliance. Bringing these together in a unified dashboard requires effort but is necessary for streamlined operations.
3. Data Privacy and Security
Digital tools store sensitive contractor data, often in the cloud. Any security breach could lead to legal and reputational issues. HSE teams must collaborate with IT to ensure strong cybersecurity and compliance with global privacy regulations.
4. Budget and Resource Constraints
Implementing digital solutions involves upfront investments in software, hardware, and training. For smaller food manufacturers, these costs can be limiting. Training staff also takes time away from daily responsibilities. Balancing cost, risk, and safety benefits is key.
What the Future Holds: Innovations in Contractor Management
Over the next five years, new technologies will help food manufacturers improve safety, ensure compliance, and enhance contractor performance.
1. Advanced AI and Machine Learning
AI and machine learning will become more advanced, offering precise forecasts of safety risks and resource needs. These tools will continually learn from past incidents to improve predictions and safety strategies.
2. Augmented Reality (AR) for On-Site Training
AR tools—such as smart glasses and mobile apps—will deliver real-time safety training at job sites. This immersive experience will help contractors understand safety protocols through hands-on simulations. It’s especially helpful for complex scenarios like confined spaces or lockout/tagout procedures.
3. Blockchain for Transparent Records
Blockchain can create tamper-proof records of contractor credentials, safety audits, and compliance performance. This ensures transparency and real-time verification of qualifications. Additionally, blockchain can streamline payments and contract management through secure, automated transactions.
4. IoT Wearables for Worker Safety
Wearable tech connected to IoT platforms can monitor fatigue, heart rate, or exposure to hazardous materials. If a breach occurs, wearables send real-time alerts to enable quick intervention. This tech minimizes risk and improves response times.
5. Mobile-Ready Worker Pass Solutions
Integrated Worker Pass tools will soon combine security, training records, insurance, equipment status, and qualification data. This creates a one-stop interface for real-time verification and on-the-spot updates. It simplifies safety checks and boosts efficiency across sites.
6. Smart Performance Dashboards
Contractor management platforms will soon feature enhanced dashboards that pull data from IoT devices, training logs, compliance tools, and AI systems. These dashboards offer real-time insights into contractor safety and compliance performance. They help HSE teams act quickly to prevent incidents.
How Food Manufacturers Benefit from Digital Solutions
Digital platforms are helping food manufacturers gain control over contractor safety and compliance. From real-time alerts to predictive analytics, these tools reduce risks and improve decision-making.
Moreover, cloud-based systems offer scalability and standardization. Whether operating one facility or many, manufacturers can manage safety data across sites in a unified manner. This fosters consistency and reduces compliance gaps.
Digital solutions also help streamline audits. When contractor documentation is centralized and up to date, HSE teams can easily produce required records for internal or regulatory reviews.
In addition, automated workflows improve efficiency. Instead of manually chasing certifications or training completions, teams receive alerts when actions are required. As a result, food manufacturers can spend more time focusing on prevention rather than reaction.
Overcoming Implementation Roadblocks
To fully benefit from digital transformation, food manufacturers need a solid implementation strategy. That includes selecting user-friendly platforms, offering comprehensive training, and providing ongoing technical support.
Leadership support is also crucial. When leadership communicates the value of digital tools—and models their usage—contractors and employees are more likely to adopt them.
Collaboration between departments is another success factor. HSE, IT, legal, and operations teams must align to ensure digital platforms meet safety, security, and business needs.
Lastly, feedback loops should be built into the implementation process. Gathering input from frontline users helps refine tools and ensures the platform delivers value.
Conclusion
For food manufacturers, the future of contractor management lies in digital solutions. These tools are reshaping how HSE teams approach safety, compliance, and performance monitoring.
While there are challenges in integrating new technologies—such as change resistance, budget constraints, and system compatibility—the long-term benefits are clear. Real-time monitoring, predictive insights, efficient onboarding, and better training create safer work environments.
Looking ahead, innovations like AR training, AI forecasting, and blockchain verification will further enhance contractor management. Wearables and mobile platforms will give HSE teams more visibility and control than ever before.
Ultimately, digital transformation isn’t just about technology—it’s about building safer, smarter, and more compliant workplaces. For food manufacturers aiming to stay competitive and meet evolving safety standards, digital contractor management is no longer optional. It’s essential.
About the Author
Dr. Simon Goncharenko, PhD, CSP, CSHO is the Director of EHS at Veriforce, LLC, and member of the Veriforce Strategic Advisory Board. Having been born and raised in Eastern Europe, Simon’s 30 years of professional experience have seen him lead teams on three continents and in various industries, including oil and gas, construction, and data centers.
His most recent employment prior to Veriforce was with Meta Platforms, Inc. formerly Facebook, where Simon supported construction of multi-billion-dollar hyperscale AI data centers. Dr. Goncharenko has authored or contributed to over 80 articles, including in the Professional Safety Journal, and 6 books, including Save Lives: Pushing Boundaries in Human Factors, and Operationalizing Safety for Today’s World: A Humancentric Practical Guide. The companion training to the book, entitled Save Lives Global Human & Organizational Factors©, the world’s first and only human factors program designed specifically for the operators, builders, and contractors of mission critical facilities, has been widely popular with hundreds of participants around the globe. Simon is an animated and engaging professor and Master Trainer, charismatic keynote speaker, and podcaster of the Save Lives Global Podcast.