
How the FDA’s New Food Traceability Regulations Impact F&B Companies
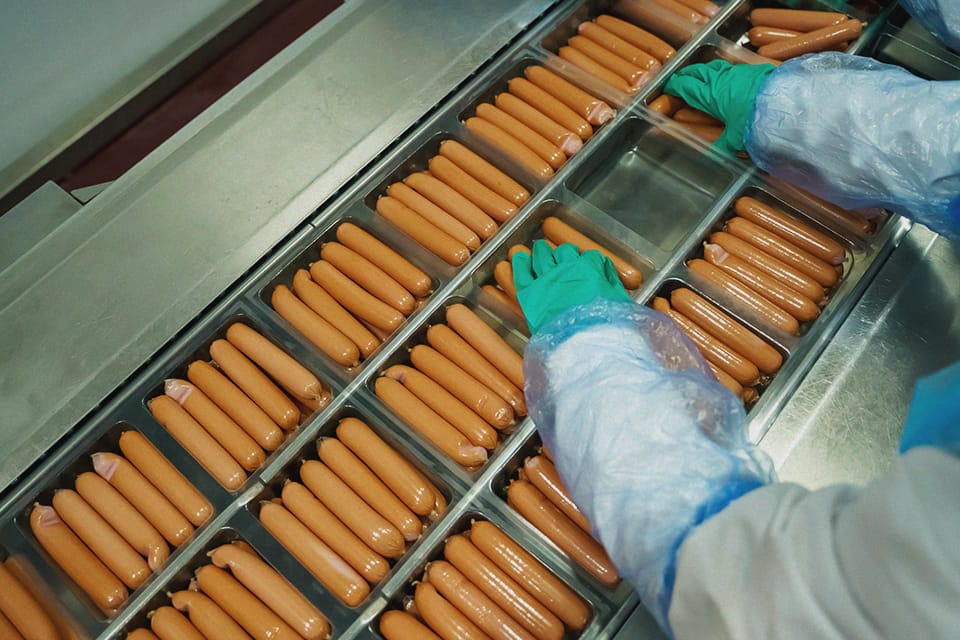
The US Food and Drug Administration’s (FDA) Food Traceability Final Rule introduces significant changes that food and beverage companies must adapt to. Focused on improving food safety, the rule emphasizes detailed recordkeeping for specific foods on the Food Traceability List (FTL). For manufacturers and distribution centers, compliance with these regulations is crucial to maintaining operational integrity and consumer trust.
What is the FDA’s Food Traceability Final Rule?
The Food Traceability Final Rule, part of the FDA Food Safety Modernization Act (FSMA), sets requirements for additional traceability records across the supply chain. The rule mandates detailed documentation of Critical Tracking Events (CTEs) — key points where food is handled or transformed — and associated Key Data Elements (KDEs). Foods on the FTL, like leafy greens, seafood, and certain cheeses, require particular attention.
Compliance enables faster identification and removal of potentially contaminated foods from the supply chain, reducing foodborne illnesses and deaths. All entities, including those manufacturing, processing, packing, or holding foods on the FTL, must provide traceability data to the FDA within 24 hours upon request.
With a compliance date of January 20, 2026, now is the time for food and beverage companies to prepare for these changes.
How the Food Traceability Rule Affects Distribution Centers
Distribution centers play a pivotal role in the supply chain, acting as intermediaries between manufacturers and retailers. The food traceability rule requires distribution centers to maintain detailed records of foods they handle. This includes assigning and tracking traceability lot codes (TLCs) and documenting KDEs for every shipment.
Key impacts for distribution centers include:
- Enhanced Recordkeeping: Distribution centers must store traceability data in a format accessible to the FDA within 24 hours.
- Streamlined Communication: Facilities need to share traceability data with supply chain partners, ensuring KDEs follow products from origin to destination.
- Integration of New Technology: Many centers will need to upgrade systems to handle the additional data requirements effectively.
By improving food traceability, distribution centers not only comply with regulations, but also enhance operational transparency and efficiency.
How the Food Traceability Rule Impacts Manufacturers
For manufacturers, compliance with the food traceability rule is equally critical. Beyond meeting legal requirements, adherence signals a commitment to consumer safety and supply chain accountability.
Assigning Traceability Lot Codes
Manufacturers must assign unique TLCs to foods on the FTL during specific processes, such as initial packing or transformation. These codes link a product’s journey across various CTEs, ensuring end-to-end traceability.
Developing Comprehensive Traceability Plans
The FDA requires manufacturers to maintain a written traceability plan outlining their compliance strategies. The plan should include:
- Procedures for recording and storing KDEs.
- A method for assigning TLCs.
- Designated contacts for traceability-related questions.
- Farm maps or aquaculture container locations for applicable entities.
Having a robust traceability plan ensures manufacturers are prepared to respond to FDA inquiries or potential recalls quickly.
Collaboration with Supply Chain Partners
Manufacturers must align their practices with those of suppliers and distributors to ensure seamless traceability. This includes agreeing on standardized documentation formats and sharing traceability data electronically when possible.
Benefits of Improved Food Traceability
The FDA’s focus on food traceability is not just about regulatory compliance — it’s about fostering a safer food system. Enhanced traceability reduces the time it takes to identify and remove contaminated foods from the market. This limits the spread of foodborne illnesses and mitigates the financial and reputational damages of recalls.
Moreover, better traceability systems offer additional benefits for manufacturers and distributors:
- Operational Efficiency: Digital systems streamline data tracking and reduce manual errors.
- Consumer Confidence: Transparency about a product’s journey builds trust with end-users.
- Competitive Advantage: Companies that adopt advanced traceability measures position themselves as industry leaders in food safety.
Challenges in Implementing the Food Traceability Rule
While the benefits are clear, compliance with the food traceability rule presents challenges:
- Data Management: Handling the volume of data required for KDEs and CTEs can be overwhelming, especially for companies relying on outdated systems.
- Training and Education: Employees across the supply chain need to understand the new requirements and their role in maintaining compliance.
- Coordination Across the Supply Chain: Ensuring all partners, from farmers to distributors, align on traceability practices requires significant effort.
Despite these hurdles, early preparation can ease the transition and ensure compliance by the 2026 deadline.
Preparing for Compliance: Practical Steps
To navigate the complexities of the Food Traceability Final Rule, food and beverage companies should:
- Conduct a Compliance Audit: Assess existing practices to identify gaps in traceability recordkeeping.
- Invest in Technology: Implement traceability software capable of capturing and storing KDEs for each CTE.
- Engage Supply Chain Partners: Open communication with suppliers, distributors, and retailers is essential for cohesive compliance.
- Develop a Traceability Plan: Create a detailed plan that aligns with FDA requirements, including clear procedures for managing KDEs and TLCs.
- Train Employees: Ensure all staff understand the new regulations and their role in compliance.
By taking these steps, companies can meet regulatory requirements while enhancing overall supply chain efficiency.
Why Food Traceability Matters More Than Ever
The food traceability rule underscores the importance of safety and transparency in today’s food supply chain. With increasing consumer demand for accountability, the rule provides a framework for companies to meet these expectations while safeguarding public health.
Improving food traceability also equips businesses to respond swiftly to potential crises, minimizing financial and reputational risks. As the January 2026 compliance deadline approaches, companies must act now to ensure they are prepared.
Veriforce’s Food & Beverage Solutions
Adapting to the FDA’s Food Traceability Final Rule is no small task, but Veriforce can help simplify the process by streamlining contractor management while you navigate new regulations. Our comprehensive compliance solutions help food and beverage companies focus on the Final Rule.
We can ease the operational burden of the new rule by ensuring you have:
- Prequalified contractors
- Safety training for workers
- Insurance verification, where we do the bulk of the work.
- Worker-level compliance and site access controls
Take the next step towards compliance today.
Contact us to learn how we can help.