
5 Critical Components and Best Practices of Subcontractor Management Programs
During Veriforce’s Select Client Series event on April 22, 2022, Dr. Linda Martin (SafeLand) hosted a panel discussion on “Critical Components and Best Practices Subcontractor Management.” Joining Dr. Martin for the guided discussion were four industry experts, Mr. Richard Emberling (Veriforce), Mr. Bill Walker (Batallion Oil), Mr. David Bates (OSHA Area Director – Ret.), and Mr. Harris Neely (Aethon Energy).
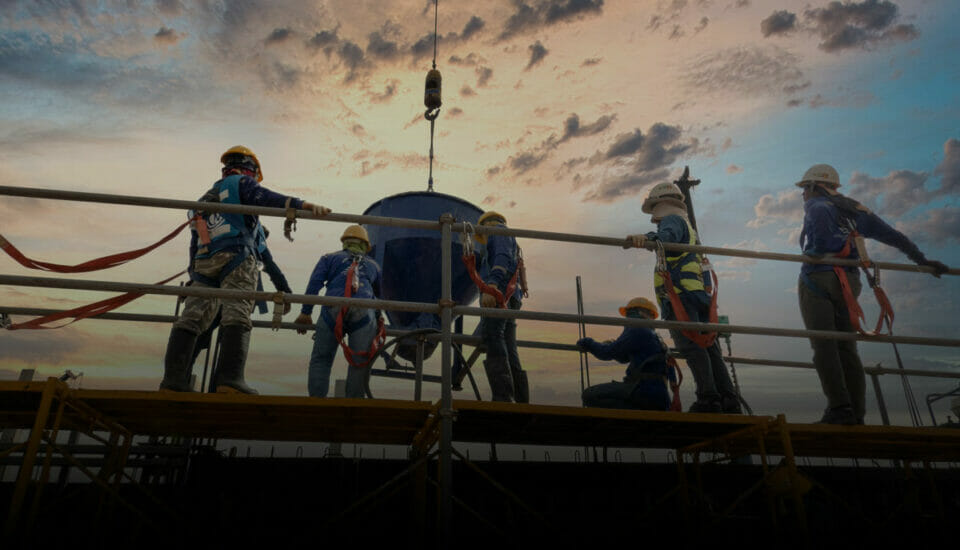
During Veriforce’s Select Client Series event on April 22, 2022, Dr. Linda Martin (SafeLand) hosted a panel discussion on “Critical Components and Best Practices Subcontractor Management.” Joining Dr. Martin for the guided discussion were four industry experts, Mr. Richard Emberling (Veriforce), Mr. Bill Walker (Batallion Oil), Mr. David Bates (OSHA Area Director – Ret.), and Mr. Harris Neely (Aethon Energy).
The experts were asked to provide comments and opinions on several areas of subcontractor management based on their experience and personal practice philosophies. During the 60-minute discussion several focus areas were explored.
1. Pre-Qualification
Current best practice is to use third-party prequalification services to help contractors identify gaps in subcontractor safety management systems and assist in quantifying potential risk. Prior to the use of these services, companies relied on company-generated paper-centric submissions that needed to be reviewed by safety and health, risk, and procurement personnel.
Panel members were quick to note that pre-qualification by third-party services provides a baseline, but that in depth work needs to be done by the hiring client to “trust but verify” submissions made to these systems by performing document review and on-site audits if a subcontractor is hired to perform work.
2. Procurement
Contract language should be used to set clear mandates for subcontractor regulatory compliance and safety expectations, among other things. However, while clear contract language can serve as a minimally effective way to limit liability for the hiring client and enumerate the non-negotiable expectations and responsibilities of subcontractors, risks related to working together on a project will always still exist. However, shared responsibility is the new normal for managing safety between hiring clients and subcontractors.
Per OSHA, on multi-employer worksites more than one employer may be citable for a hazardous condition that violates an OSHA standard. This fact should encourage hiring clients to seek out ways to work proactively with their subcontractors to plan, execute, monitor, audit, and continuously improve all aspects related to the safety and wellbeing of workers and the proactive mitigation of hazards. Hiring clients should couple pre-qualification measures to procurement, but not lose site of the necessity for combined safety excellence with subcontractors throughout the project life-cycle.
3. Project Life Cycle
It is important to be aware that any subcontractor that comes onto a hiring client’s site is immediately part of their risk profile. Management of subcontractors should be accomplished as a continuous process throughout the project and subcontract lifecycle. Understanding specific tasks in managing the subcontract, as well as requirements and assignment of responsibilities during each lifecycle phase, will aid ensuring compliance targets are met, safety is a priority, and workers are being protected.
Planning, communication, and collaboration surrounding continuous safety improvement is essential to facilitating a comprehensive focus on occupational safety and health risks for all affected worker groups across all project life cycle stages. It is not enough to “set it and forget it” when it comes to safety programs, orientation, training, site conditions, and other important aspects of keeping all site workers out of harm’s way. Safety is an action in motion, not a set condition.
4. Performance Metrics
Hiring clients can use various performance metrics to help assess their subcontractor’s adherence and commitment to safety and health program effectiveness at a site. These metrics include lagging indicators, such as OSHA injury and illness recordkeeping data, insurance modification rates, and worker’s compensation claim losses. These metrics are often adopted into pre-screening techniques for evaluating contractor and supplier risk levels.
Conversely, the experts agreed that gathering performance data and evaluating trends of safety incidents and near misses during the life of the project allows for the ongoing and timely review of trends in a subcontractor’s safety and health. Frequent, timely and in-depth review of incidents, discussions about continuous improvements to processes and programs, and communication of lessons learned to all site parties serve to improve overall project safety and decrease risk.
5. Teamwork
When it comes to safety and risk, teamwork is a vital component of a hiring client and subcontractor relationship. Proper planning, definition of the goals and objectives, assignment of roles and responsibilities, and collaborative work processes, all are critical when it comes to preventing incidents and injuries related to the accomplishment of projects. Some ways that a hiring client can foster teamwork without taking on additional liability is to provide coaching and teachable moments to make suggestions on improving safety programs and work practices.
While teamwork is generally a site-specific mix of shared trust and ownership, it is advisable to stay cognizant that a strong distinction should be made between providing a hiring client’s coaching efforts aimed at helping subcontractors improve their safety programs and performance and telling a subcontractor what to do or how to do a task. However, the most successful hiring client-subcontractor relationships will show open communication, clarity of expectations, and concern for the overall safety of the workers collectively accomplishing a job.
Summary
It is important for hiring clients to take charge of the project safety objectives and view their subcontractors as valued partners during the life cycle of projects and the wellbeing of all workers. Although it takes a little more effort and forethought for the hiring client to become an active participant in project safety management and the subcontractor’s safety compliance and growth, the increased involvement is generally rewarded with risk reduction, accident avoidance, and injury prevention.