
Understanding Your Total Cost of Risk Through the Lens of Process Safety Management
Many organizations have resisted automating their risk management practices. It’s comfortable to maintain the status quo – often a combination of spreadsheets, emails and internal drives – to manage all facets of risk, including contractors. Unfortunately, there are several trade-offs.
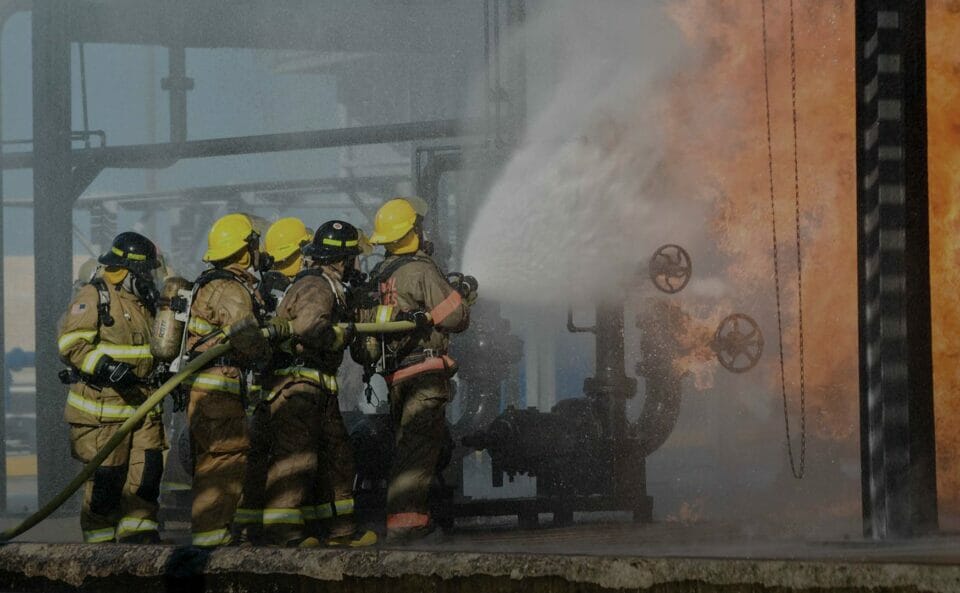
Thousands of incidents involving toxic substances harm and kill workers — and the public — every year. According to the U.S. Department of Labor, exposure to harmful substances and fires/explosions are the fifth and sixth leading causes of workplace fatalities, respectively.[1]
Warnings ignored. Negligent safety review and analysis. Operator error. Whether it be a petroleum refinery, or a dairy processing plant, use of chemicals in manufacturing mandates OSHA’s PSM,[2] or Process Safety Management, controls that enforce chemical facility safety and security.
The main challenge for manufacturing businesses is how to implement and manage the 14 principles of PSM, as many are complex and OSHA doesn’t specify how manufacturers should achieve compliance — only that they must. And that’s where things get complicated.
Implementing PSM Across Your Contingent Workforce
Of the 14 PSM elements, one of the more complex items is “Contractor Training.” Just like employees, your contractors need to be well-informed of the risks involved in their work with chemicals and the importance of following your business — and OSHA’s PSM — safety protocols.
Most contract workers cycle in and out, appointed to different job sites, filling in temporarily as needed. This creates a chasm of safety and skill accountability across your workforce.
Take a typical oil refinery. The workers toil fast and hard, and don’t necessarily know each other. Maybe they’ve worked together before, or maybe they’ve never met. And yet the skills of one directly affect the safety of the other. Some are tired. Some traveled far to get to the job site. Some are younger, less experienced. Others are older, with varying degrees of skill. In a combustible environment, this type of variation can be highly explosive — literally.
When Refinery A needs to be serviced, the entire module is taken offline and the contract crew, who worked there for the last month, is moved to another refinery. Once Refinery A is back up and running, a new crew of 1,500 workers shows up. Do you know which workers need to be trained on the new equipment, and which know the protocol? Without an effective contractor management system, there’s virtually no way of knowing.
Do You Know the Risk Profile of Your Contractor Firms?
The first step to assessing your total cost of risk (TCOR) is to get a handle on the engagement of your contract services firms. Which companies are bringing their contingent workforce to your jobsite? What work are they doing? And, most importantly, what is the contract firm’s risk profile?
Know these three things about each contractor firm working on your site:
- What is the contractor’s historical safety record?
Does the contractor firm have an acceptable safety history for the work you’re asking them to do? Washing windows on a first floor versus working in a small area with combustible materials will each carry a very different risk profile. Calibrate your health and safety expectations based on the contractor’s safety records. Taking this one step further, it’s one thing to know the contract business’ safety record, but is the crew that’s sent to your site the one that had a recent safety incident, or are they the group that didn’t? - Are they backing their safety claims up with current best practices?
Many contractors will proclaim their goal of zero safety incidents, but what processes do they have in place to get there? Do they offer regular safety training programs? Do their workers wear PPE and maintain it properly? The contractor’s safety principals will be a leading indicator of their compliance. Taking this one step further, how do you know that the actual crew showing up to your job site has completed the trainings the contractor provides? - Are they properly insured?
Irrespective of past performance and current policies and procedures, bad stuff still happens – no matter how skilled your contractors are. When a safety incident does happen, does the contractor firm have the necessary coverage? Can you transfer your risk of an accident to them?
Without a system and process designed to capture, verify, analyze, and share insights into the contracting company and their individual workers, it’s nearly impossible to understand your business’ TCOR — or your PSM compliance.
Worse yet, if an OSHA auditor shows up at your manufacturing plant, and they know that 20% or even 30% of your workforce is made up of contractors, they’re going to ask for proof of PSM application across your contingent workforce.
Then, what will you say?
[1] Bureau of Labor and Statistics, U.S. Department of Labor. https://www.bls.gov/news.release/pdf/cfoi.pdf
[2] OSHA PSM. https://www.osha.gov/process-safety-management/sbrefa
For 30 years, Veriforce has helped hiring clients and contractors understand regulatory requirements and compliance; reducing worksite risks.