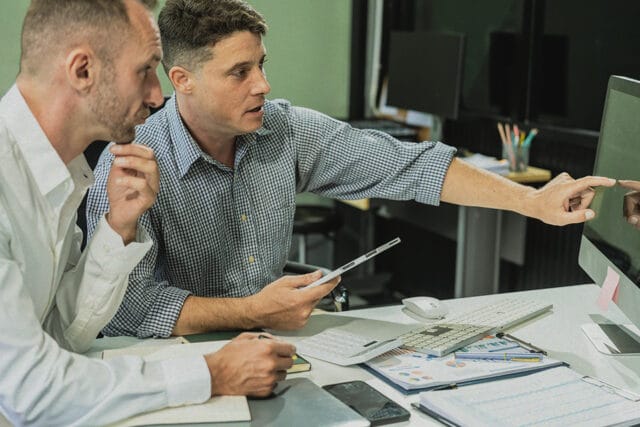
The Crucial Ingredient to Pipeline Safety: Creating a Culture of Safety, From the Top Down
Pipelines keep neighborhoods safe by transporting oil and gas underground, rather than on roads and railways. And yet when they do happen, pipeline accidents can be devastating. Create a culture of safety from the top down in pipeline construction with these three best practices.
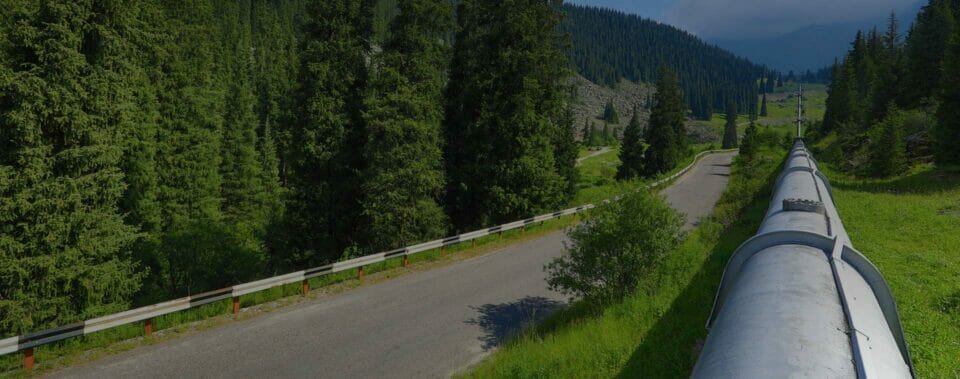
The U.S. and other modern global powerhouses rely on pipelines to transport energy products safely. While transporting oil and gas via pipeline has resulted in recent high-profile accidents, doing so on our roads and railways would be significantly more costly and dangerous to the population. Instead, our pipelines must remain safe to transport our energy where it’s needed.
Like other skilled industries, the oil and gas pipeline sector is being hit hard by a changing global workforce, making it difficult to find skilled workers to build and maintain a healthy workforce. This has led to greater danger for pipelines. If you look at the latest incident records and their sheer numbers, you’ll notice pipeline incidents have gone done in recent years. And yet, there’s not much comfort to be gained, as most of the incidents that have occurred happened in pipelines installed within the last 10 years. That tells me we’re currently struggling with quality, a direct result of the changing global workforce.
Create a Culture of Safety Across Your Workforce, from the Top Down
Pipeline employers are feeling the pressure to ensure their workers not only possess the right skills for the job but have the knowledge and controls in place to do their job safely. And this doesn’t just mean full-time employees, but contractors as well.
Of course, this is easier said than done. Here are three key elements to creating a safe and supportive environment for pipeline workers, that promotes safety from the top down:
1. Allow workers to fail, safely.
Failure is inevitable, no matter what industry you’re in. However, when employees are working with high-pressure equipment such as pipelines, failure comes with increased risk. This does not mean that your employees should be afraid to fail. Instead, management is responsible for investing more time and resources into creating an environment in which employees feel confident in their safety, even when things go wrong. Safety must come before the job, and this sentiment should be clear through your company’s values, onboarding, training, on-the-job practices, and through the actions of your leadership. Employees should trust management so that if and when a mistake is made, they are protected. Examples of innovations that are helping companies put safety first include wearables that detect and warn electricity workers of high voltages, and data-driven fault detection systems that allow operators to model and overcome fault scenarios.
2. Encourage reporting.
By decriminalizing mistakes, and making space for failure, companies can avoid inaccurate incident rates due to a lack of reporting. Whether due to fear of consequences or a company safety-incentive program, a lack of reporting is often the result of a company’s culture valuing productivity over safety
While the Occupational Safety and Health Administration (OSHA) has warned against safety-incentive programs in the past as they could deter employees from reporting incidents, it has also provided examples of incentive programs that promote safety. These include programs that reward workers “for reporting near-misses or hazards and encourage involvement in a safety and health management system.” Rate-based incentive programs are permissible as well if they do not discourage reporting.
3. Start with management.
An accessible and high-tech safety management system, organized training program and company-wide communication about the importance of safety can all go a long way in building a strong safety awareness at your organization. However, the crucial ingredient needed for these strategies to be effective is the human element.
A company’s culture is determined by its leadership— and not by what they say but on how they act and respond to the daily happenings on the job. If leadership creates a cohesive environment where safety is incorporated into all facets of operations – from hiring to procurement to production and beyond, they aren’t just creating a safety culture for their company but instead, a company culture built on safety.