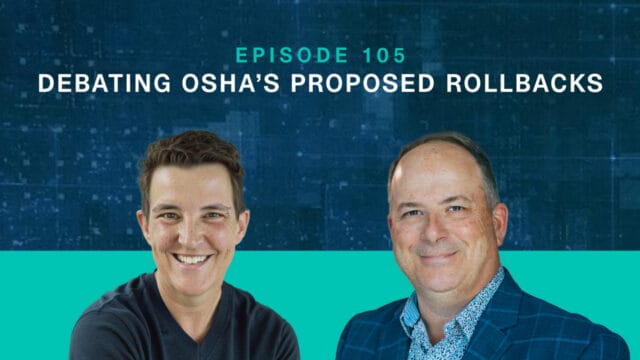
Season 2 Kickoff: Debating OSHA’s Proposed Rollbacks | The Risk Matrix Episode 105
THE RISK MATRIX Cutting-edge podcast on occupational safety and risk management. Hosted by industry titans: JAMES JUNKIN, MS, CSP, MSP,…
Not properly vetting your subcontractors can cost you. Past OSHA cases demonstrate how this can easily happen if you don’t have a process in place to ensure subcontractors have the skills and experience to get the job done safely.
Not properly vetting your subcontractors can cost you. Past OSHA cases demonstrate how this can easily happen if you don’t have a process in place to ensure subcontractors have the skills and experience to get the job done safely.
A college dorm was under construction in Little Rock, Arkansas, and upon inspection, OSHA compliance officers discovered there were fall hazards on a scaffold involving subcontractor employees. A citation was issued to the general contractor because they were not taking reasonable care to ensure the subcontractor was complying with OSHA scaffolding standards to eliminate the hazards. The subcontractor was issued citations as well. The serious violation penalty was $4000.00. That doesn’t seem like much. But the employer contested the citations, resulting in multiple levels of costly litigation that followed. The OSHA citation was appealed to the OSHA Review Commission and eventually to the United States Circuit Court of Appeals where the result was in favor of OSHA setting a precedent for OSHA’s ability in the future to issue citations to general contractors as controlling employers under its multi-employer worksite policy. While the cost of the citation wasn’t much, the costs in legal fees were substantial.
This entire scenario may have been prevented by comprehensively vetting and managing subcontractors.
Having multiple employers at a jobsite can be complex and unsafe, unless steps are put into place to manage risks and prevent serious incidents. Vetting subcontractors is a crucial step for any project and failure to do so could cause serious incidents, costing you your reputation and even your business. With the current supply chain and skilled labor shortages, it is even more important to perform robust vetting of subcontractors in today’s job markets. When you have subs of subs, things can get really dicey and out of control, very quickly.
Having complete visibility into your entire supply chain is critical so it’s important that hiring clients work very closely with both prime contractors and subcontractors to ensure requirements are being met at all levels of the project.
A subcontractor management plan is important for employers for many reasons because, from an OSHA perspective, it demonstrates their commitment to the health and safety of their employees. With each OSHA audit and inspection, they’re going to evaluate companies on how detailed and thorough they are in ensuring that their job site is safe. Without even getting into the liability issues of how that affects the prime contractor it also matters to OSHA how they’re managed, to ensure they’re enforcing health and safety rules and requirements.
Here are just a few things OSHA looks for when they arrive at your jobsite:
If prime contractors are not enforcing requirements, they are susceptible to being issued citations through the Multi-Employer Citation policy. Multi-employer worksites can be complex and OSHA compliance staff conducting inspections evaluate if prime contractors are taking reasonable care to ensure all contractors under their control are complying with OSHA regulations and company safety policies. Ideally, there is a system in place for everyone on the jobsite to ensure they are working together and there is someone in charge to ensure the system is working properly.
Companies like Veriforce can help you navigate the complexities of multi-employer worksites by giving you full visibility into your supply chain. At the end of the day, we all need to keep risk reduction a top priority and ensure workers get home safely from high hazard jobs.
THE RISK MATRIX Cutting-edge podcast on occupational safety and risk management. Hosted by industry titans: JAMES JUNKIN, MS, CSP, MSP,…
We’ll send you practical and insightful supply chain risk management info that can benefit your business. Plus, important company updates that keep you in the loop.