
Plan, Do, Review: Enhancing Safety by Implementing the Best Processes
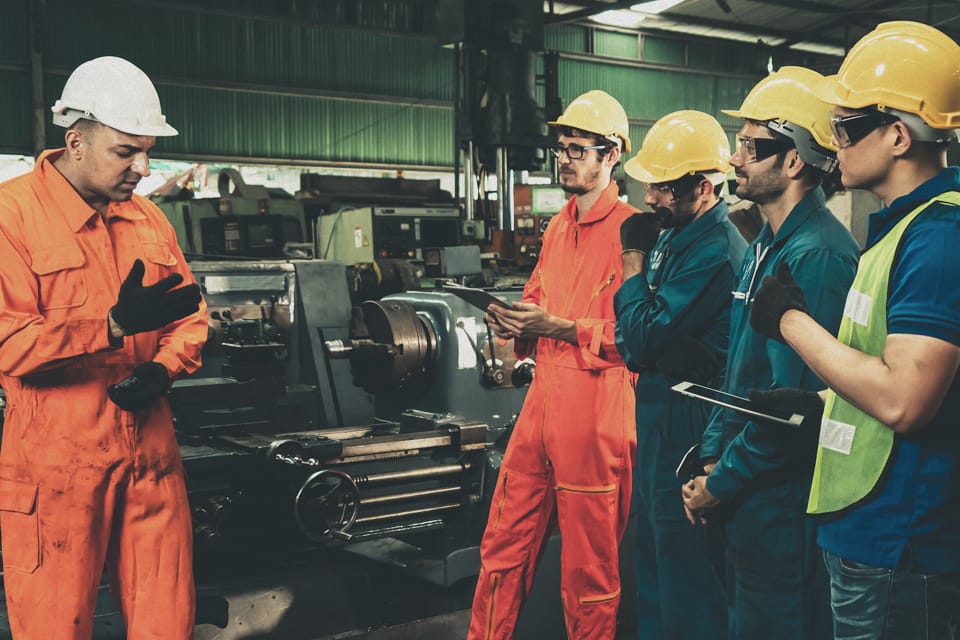
The “Plan, Do, Review” cycle is critical for safety professionals looking to avoid wasted energy, boost productivity, and safeguard workers from harm. It helps companies identify and control their health and safety risks, reduce incidents, and consistently improve performance.
However, not everyone understands the cycle’s importance or how to deploy the best process, and missing out on this strategy can expose workers to added and unnecessary risk.
This article discusses the Plan, Do, Review (PDR) concept to help those companies get started, lays out steps for implementing a plan, and how a company might review the results based on its initial objectives.
What Is the Plan, Do, Review Cycle?
The PDR cycle is an ongoing, continuous loop of planning, doing, and reviewing designed to improve processes, boost safety, and eliminate recurring mistakes
Why Is It Important?
This approach focuses on ongoing improvement. It’s a way to keep pushing forward and ensure the working environment is safer and more productive. It provides an effective means for solving ongoing safety problems and managing change on the worksite.
Creating an Effective Plan (the “Plan”)
The steps for creating an effective plan might include the following:
Breaking Down Objectives into Achievable Steps
The first phase of creating a strategy involves breaking down goals into steps. Teams accomplish this by dissecting larger, overarching goals into more manageable tasks.
Dividing objectives into action items facilitates clarity in direction and aids in supporting progress.
Assigning Roles and Duties
The stage entails assigning roles and duties. Who will handle each task? Who will hold team members accountable and ensure they are making progress?
This phase marks the beginning of planning. Team leaders should ensure that everyone understands their responsibilities and deadlines and knows who oversees the process to keep everyone aligned with the plan.
Establishing Timelines and Milestones
The next step is breaking down the plan into steps with specific completion dates. This process requires pinpointing significant markers indicating the team is progressing successfully.
Setting clear timelines and milestones can really boost everyone’s motivation and keep the project on track. Safety managers should remember to celebrate achievements as they are reached. Recognizing progress keeps everyone excited and engaged with the team’s work.
Implementing the Plan (the “Do”)
After laying out the plan, it’s time to put it into action, and doing so might include the following steps:
Sharing the Plan with the Team
The first step in executing a plan is to communicate it to everyone. It’s crucial for all team members to be informed and understand their responsibilities. This means ensuring that each team member is aware of their tasks, deadlines, and the significance of their roles.
Showing them how their contributions can positively impact the company’s performance is essential.
Tracking Progress and Adjusting as Needed
After the plan has been relayed to the team and executed, team leaders should monitor progress and adjust the process whenever necessary.
They should identify what milestones they’ve achieved and confirm that everything is going according to schedule. If it is not, they must decide on what adjustments are required.
One advantage of using the PDR method is that it promotes progress and continual improvement.
Overcoming Obstacles and Challenges
Every plan faces challenges, and teams may encounter hurdles and difficulties during the process. However, teams can gain an advantage by identifying those challenges and devising a plan to address them.
The strategy for designing that plan should include welcoming ideas from the workers on the ground because they’re the ones involved in the daily processes. Team leaders should encourage members to think creatively and collaborate to find answers.
Reviewing and Evaluating Results (the “Review’)
The teams have planned and executed. Now it’s time to review and evaluate the results. This is where management takes a step back and sees how far they’ve come.
Measuring Success Against Goals and Objectives
The initial step should be checking if they’ve achieved their targets based on set company goals and objectives. Have they reached all of them or missed some points? What could be the reasons for any gaps?
Now’s the time to put those precise goals they created into action. Safety managers should analyze how well teams did compared to their goals. As always, they should not overlook the team’s thoughts and ideas.
Identifying Areas for Improvement
Even if a company hits all its safety goals, there’s still room for growth. Management should use the review and evaluation steps to spot areas that could improve in the future.
Maybe a step in the plan didn’t quite work out how they thought it would. Or maybe there was an obstacle no one anticipated. Whatever it is, companies should use this as an opportunity to learn and grow.
Creating the Best Plan, Do, Review Process Requires Top-Notch Safety Training and Coaching
The Plan, Do, Review cycle isn’t just a one-time solution; it’s a continuous process that fosters a culture of safety and continuous improvement. By embracing this ongoing cycle, companies can proactively manage risk, empower their workforce, and create a safer, more productive work environment for everyone.
However, establishing the best possible PDR process requires first receiving the best possible training to ensure you and your team have the tools necessary to do the job safely and efficiently.
We understand your need to make sure your operations are efficient. That’s why we partnered with WorkSafe-Texas, which helps small businesses in the Austin, Dallas, and Houston Metro areas develop effective Plan, Do, and Review processes.
Contact us today to learn more.
Click here to learn more about WorkSafe-Texas.