
Managing Safety Risks in Food Production: A Focus on Contractor Safety Protocols
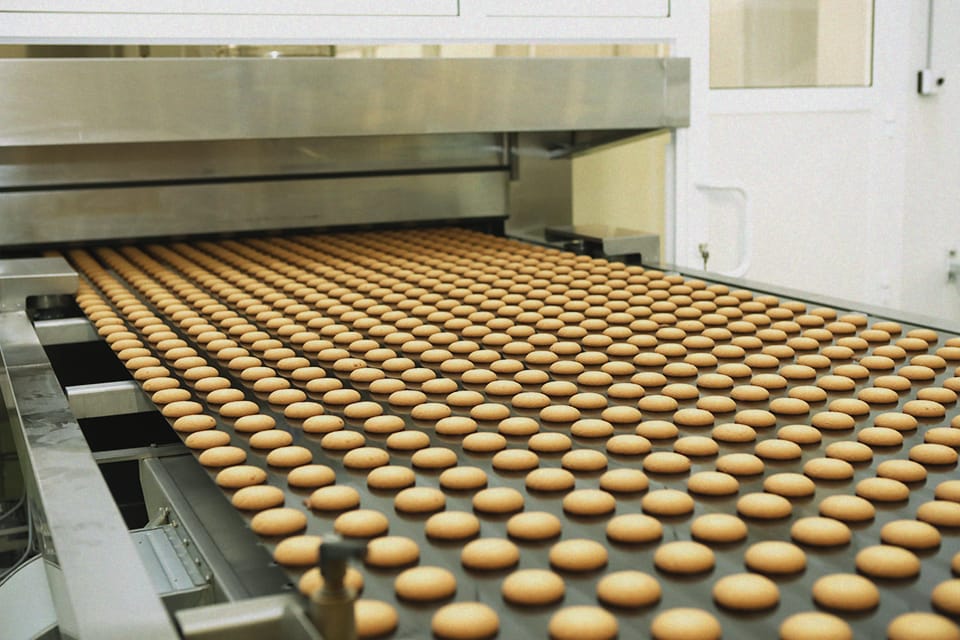
As the global food production industry continues to expand to meet growing consumer demand, manufacturers face increased challenges in maintaining safety and quality standards. Food production often involves contractors for maintenance, construction, and logistics tasks. While this supports rapid scaling, it introduces risks like contamination, equipment failure, and workplace incidents. Addressing these risks effectively is crucial to preventing disruptions in production and distribution.
This article explores how proactive contractor safety protocols are essential for mitigating these risks in food production.
Understanding Safety Risks in Large-Scale Food Production
The increasing complexity of the food production and beverage supply chain requires manufacturers to expand their operations. This growth often involves contractors with specialized skills but also broadens the range of safety challenges in large-scale food production.
Major Safety Risks
1. Contamination: Contractors working across multiple sites may inadvertently introduce contaminants if strict hygiene protocols are not followed. This risk is greater in facilities processing perishables or sensitive production environments.
2. Equipment Failure: Contractors responsible for equipment installation or maintenance face risks of malfunctions. This can lead to production halts, safety hazards, and financial losses.
3. Workplace Incidents: Fast-paced food production operations can lead to accidents if safety measures are not consistently enforced. Contractors unfamiliar with site-specific protocols are particularly vulnerable.
Ensuring Protocol Compliance Across Contractor Teams
To manage risks effectively, manufacturers must implement robust safety protocols and ensure contractor compliance. This starts with pre-qualification, site-specific orientation, and verification of contractor training programs tailored to their roles. These programs should address each facility’s unique safety needs.
Effective Strategies for Risk Management
1. Comprehensive Induction and Training Programs: Contractors should undergo site-specific training that focuses on safety requirements. Programs must cover hygiene standards, emergency procedures, and equipment handling. Regulatory requirements, such as OSHA, must also be included. Training verification should be mandatory before work begins, ensuring contractors are equipped to adhere to stringent safety protocols in food production.
2. Standardized Safety Protocols: Develop standardized safety protocols across all facilities to ensure consistency. This simplifies contractor integration when working on multiple food production sites.
3. Regular Inspections and Audits: Conducting consistent safety audits and inspections ensures compliance and allows for early detection of hazards. Timely corrective measures can prevent accidents from escalating. Regular evaluations ensure safety measures are followed, such as personal protective equipment (PPE) compliance and using a hierarchy of controls to mitigate risks. Frequent audits enable manufacturers to address non-compliance and improve safety practices.
4. Utilization of Safety Technologies: Leveraging technology in managing safety risks is vital for food production manufacturers as operations expand. Safety technologies improve monitoring capabilities and support proactive risk management.
One effective technology in food production is the Internet of Things (IoT). IoT devices monitor machinery performance in real time. Sensors can track temperature, humidity, and operational status, providing alerts when parameters deviate. This capability prevents equipment failures, reducing safety risks and production disruptions.
5. Clear Communication Channels: Establishing clear communication channels is critical for effective safety management in food production. Effective communication ensures all personnel, including contractors, understand responsibilities and expectations. It is fundamental to fostering a culture of safety.
Manufacturers should implement structured communication frameworks and feedback loops to facilitate information exchange between teams and contractors. Regular safety meetings can discuss safety concerns, protocol updates, and performance metrics. These sessions encourage participation and dialogue, improving risk management strategies by identifying potential hazards.
6. Fostering a Safety Culture: A strong safety culture is essential in food production to ensure effective risk management, particularly when contractors are involved. A positive safety culture encourages individuals, from management to contractor employees, to prioritize safety, identify hazards, and minimize risks. Developing this culture involves training, leadership commitment, continuous improvement, and worker engagement.
Balancing Food Production Growth with Safety
Manufacturers must balance scaling food production while maintaining stringent safety standards. Achieving this balance ensures worker safety and product integrity.
Strategic Approaches
- Process Optimization: Improve production processes for efficiency without compromising safety. This includes investing in advanced safety-integrated machinery or redesigning workflows to minimize hazards.
- Capacity Building: Hire and train dedicated safety officers to oversee contractor operations and ensure compliance with safety procedures.
- Collaborative Partnerships: Develop partnerships with contractors by setting shared safety goals. Transparent agreements on safety expectations build mutual accountability.
Case Study: Successful Contractor Safety Initiative
A global beverage manufacturer revamped their contractor safety strategy during production expansion. Facing growing demand, the company launched the “Safety First” initiative to improve contractor safety.
- Enhanced Training Programs: Contractors completed a detailed online safety module before entering the site. The program covered all relevant safety protocols for food production and beverage manufacturing.
- Regular Safety Audits and Contractor Evaluations: Quarterly audits assessed contractor adherence to safety standards. Compliant contractors were prioritized for future assignments.
- Technology Integration: A contractor management software tracked compliance, incidents, and training completions. Centralized oversight ensured prompt corrective actions.
- Collaboration and Feedback Mechanisms: Continuous collaboration was encouraged through regular feedback sessions. These sessions fostered a shared commitment to improving safety practices.
Conclusion
In the expanding food production landscape, safety risks evolve as manufacturers engage contractors. Proactive safety management through robust protocols, training, and technology integration is essential for risk mitigation. By fostering a strong safety culture and collaborative partnerships, manufacturers can ensure workforce well-being, maintain product integrity, and achieve sustainable growth. Implementing contractor safety initiatives not only safeguards operations but also strengthens the reputation of the food production industry.
About the Author
James A. Junkin, MS, CSP, MSP, SMS, ASP, CSHO is the chief executive officer of Mariner-Gulf Consulting & Services, LLC and the chair of the Veriforce Strategic Advisory Board and the past chair of Professional Safety journal’s editorial review board. James is a member of the Advisory Board for the National Association of Safety Professionals (NASP). He is Columbia Southern University’s 2022 Safety Professional of the Year (Runner Up), a 2023 recipient of the National Association of Environmental Management’s (NAEM) 30 over 30 Award for excellence in the practice of occupational safety and health and sustainability, and the American Society of Safety Professionals (ASSP) 2024 Safety Professional of the Year for Training and Communications, and the recipient of the ASSP 2023-2024 Charles V. Culberson award. He is a much sought after master trainer, keynote speaker, podcaster of The Risk Matrix, and author of numerous articles concerning occupational safety and health.