
Proactive vs. Reactive Safety in Midstream Oil and Gas
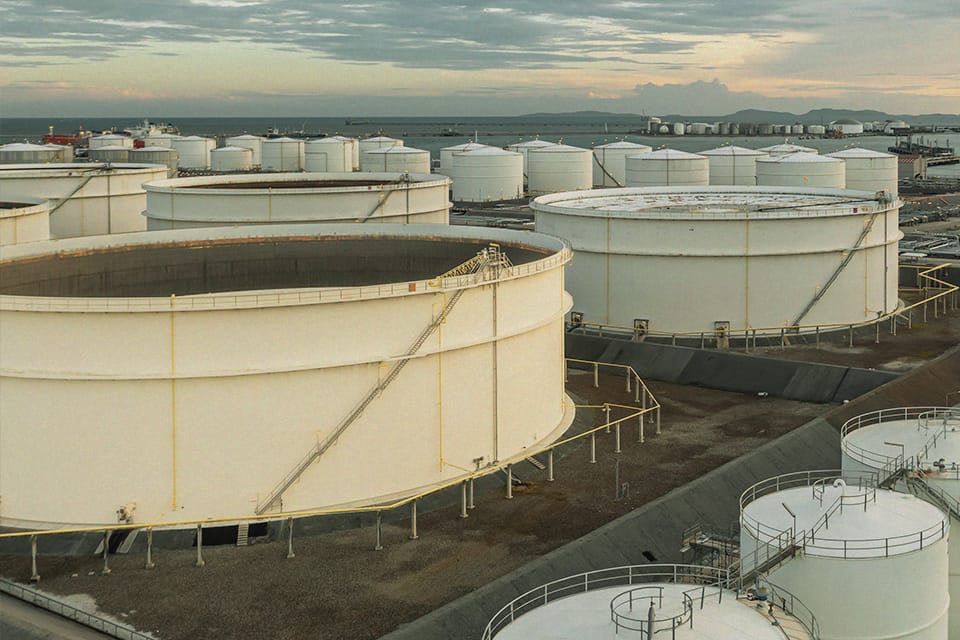
The midstream oil and gas sector is inherently risky. From the transportation of crude oil and natural gas to the processing and storage of these products, the potential for accidents and incidents is ever-present. To mitigate these risks and protect both personnel and the environment, effective safety management is crucial. Central to this is the distinction between proactive vs reactive safety approaches.
Proactive safety is all about preventing incidents before they occur, while reactive safety focuses on responding to incidents after they happen. Both are essential components of a robust safety program, but a strong emphasis on proactive measures is important for long-term success.
Proactive vs. Reactive Safety: A Fundamental Difference
Proactive safety focuses on preventing incidents before they occur. It involves identifying potential hazards, implementing control measures, and continuously monitoring safety performance. It’s like wearing a seatbelt; taking steps to avoid accidents rather than dealing with the consequences afterward.
On the other hand, reactive safety is about responding to incidents after they happen. It involves investigating accidents, implementing corrective actions, and complying with regulations. While essential, a reactive approach is inherently limited, as it doesn’t prevent future incidents.
Building a Culture of Proactive Safety
Proactive safety is the foundation of a high-performing safety culture. It involves:
Comprehensive risk assessments: Identifying potential hazards and evaluating their risks.
Employee training and development: Empowering employees with the knowledge and skills to work safely.
Preventive maintenance: Regularly inspecting and maintaining equipment to prevent failures.
Safety audits and inspections: Identifying potential hazards and compliance gaps.
Incident investigation and learning: Analyzing near-misses and incidents to prevent recurrence.
By prioritizing proactive safety, companies can significantly reduce the likelihood of accidents, injuries, and environmental damage.
The Limitations of a Reactive Approach
While reactive safety is necessary for addressing incidents, it should not be the primary focus. Furthermore, relying solely on reactive measures can lead to higher costs, damaged reputation, and legal liabilities. Think of it as putting out fires rather than preventing them from starting in the first place.
Key characteristics of a reactive safety approach include:
Incident investigation: Determining the root causes of accidents and near misses.
Corrective actions: Implementing measures to prevent similar incidents from happening again.
Compliance with regulations: Adhering to industry standards and government regulations.
Worker’s compensation: Providing financial support to injured employees.
While necessary, a reactive approach is inherently limited. It can be costly, time-consuming, and does not prevent future incidents.
Balancing Proactive vs Reactive Safety
The most effective safety programs combine both proactive and reactive elements. By integrating these approaches, companies can create a comprehensive safety management system that addresses both short-term and long-term risks.
Key strategies include:
- Leveraging incident investigations to identify proactive measures
- Continuously improving safety performance based on data
- Fostering a culture of employee involvement
- Demonstrating strong leadership commitment to safety
Overcoming Challenges in Implementing Proactive Safety
Implementing a proactive safety culture can be challenging. Common obstacles include:
Resistance to change: Overcoming resistance to new safety procedures and processes.
Resource constraints: Allocating sufficient budget and personnel for safety initiatives.
Measuring performance: Developing effective metrics to track safety performance.
To address these challenges, organizations can adopt the following best practices:
- Communicate the value of safety: Clearly articulate the benefits of a proactive safety approach.
- Involve employees: Empower employees to contribute to safety initiatives.
- Utilize technology: Leverage technology to streamline safety processes and data analysis.
- Continuous improvement: Regularly evaluate and refine safety programs.
Veriforce: Your Partner in Proactive Safety
A proactive safety approach is indispensable for the long-term success of midstream oil and gas operations. By prioritizing prevention, organizations can significantly reduce the risk of accidents, injuries, and environmental damage. While reactive measures are necessary for responding to incidents, a strong emphasis on prevention is crucial for building a culture of safety.
Veriforce is dedicated to helping midstream companies build strong safety cultures. Our proactive safety solutions include:
- Comprehensive risk assessments
- Tailored safety training programs
- Rigorous safety audits and inspections
- Expert services to guide your process
By partnering with Veriforce, you can gain access to the expertise and resources needed to implement a world-class proactive safety program.
As technology continues to advance, new and innovative approaches to safety management will emerge. By staying ahead of the curve, midstream companies can create a safer and more sustainable future.
Contact us today to learn more.