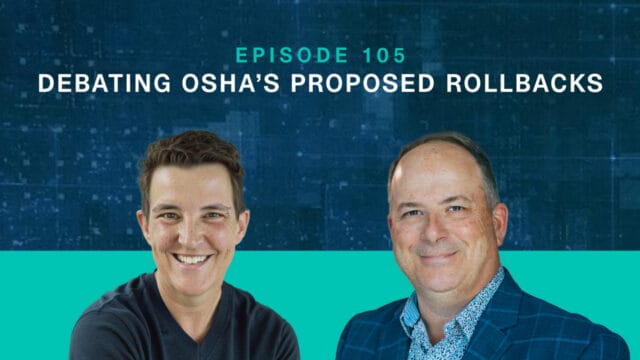
Season 2 Kickoff: Debating OSHA’s Proposed Rollbacks | The Risk Matrix Episode 105
THE RISK MATRIX Cutting-edge podcast on occupational safety and risk management. Hosted by industry titans: JAMES JUNKIN, MS, CSP, MSP,…
Proper and continuous safety training at all levels within your operation, combined with an executable safety management system that incorporates prevention through design techniques, can reduce costly and dangerous mistakes and ensure everyone understands expectations.
Workplace safety is one of the main priorities for organizations across the globe as employers try to find new ways to keep their remote, frontline, and in-office employees safe and healthy. Safety shouldn’t be an afterthought and it also doesn’t have to be associated with productivity loss. Safety and productivity can go hand in hand.
As we reconcile safety against productivity – particularly for hiring clients working with contractors who often need to be upskilled – businesses must have comprehensive safety management systems. This includes but is not limited to, planning for success, leveraging emerging technology, updating and evaluating training, and creating a culture of safety across the entire operation.
Here’s a look at effective strategies for creating an environment where workers can be both safe and productive.
Proper planning reduces the likelihood of poor performance. Successful projects don’t just happen — they require careful planning and sound risk management throughout the job. Creating a culture of “Safety through Design” depends upon identifying hazards and risks in the design and redesign phases of the work itself. Doing so results in significant benefits, such as:
A successful safety management system is centered around a safety communication plan. This consists of a set of materials that specify how workers can remain safe on the job, important company safety updates as policies and job site requirements change, and messages and other internal campaigns that need to be communicated to the right employees at the right time.
Ongoing employee learning and development is a necessity for most organizations, but particularly those in high-risk industries, from manufacturing and mining to chemicals and oil and gas. For these companies, safety and compliance training can be a requisite to their ability to operate as a business. Not only must comprehensive training take place when onboarding every new employee, it must also be provided to existing workers at regular intervals to comply with changes to existing regulations and to reinforce safe operations.
You have to train your staff on certain things, but there’s no one-size-fits-all solution and you should tailor training to the capabilities of your team. Traditionally, training has been given in a classroom setting, but COVID-19 forced a transition to instructor-led training over video conferencing, offering ways to become more efficient and flexible.
E-learning is transforming the way organizations offer training today. New tools that leverage mobile devices are making training opportunities more convenient with the ability for employees to receive instruction any time of day, at nearly any location. The use of video, microlearning, and gamification has also increased training effectiveness by creating a more interesting and interactive learning experience.
Blending a combination of e-learning tools that complement and augment traditional curriculum-based or instructor-led sessions and are customized into a program based on the unique training needs of an organization will result in a more prepared workforce and safer workplace for companies.
Don’t sacrifice retention for efficiency. Organizations should be continually evaluating the effectiveness of their training. While in-person training has traditionally been seen as most effective, a 2021 research study by CPWR, The Center for Construction Research and Training, entitled The Use of Distance Learning in Occupational Health and Safety Training: Assessing the Effectiveness and Sustainability in the Context of the COVID-19 Pandemic noted that “while face-to-face delivery was rated more highly, respondents indicated that, on average, both delivery formats were highly effective. Importantly, no significant differences in specific safety-related knowledge and skills were reported by participants in the face-to-face versus distance learning formats, suggesting that high levels of learning occurred regardless of format.”
Companies should experiment with different modalities of training, with the goal of achieving “acceptable effectiveness.”
The primary objective in evaluating any training program is to develop an understanding of whether it has achieved its objectives. Measure how employees have retained the training, if they have learned the safety material presented and if their on-the-job behavior has changed. And most importantly, measure your organization’s safety results. Then, repeat.
Safety training is not a one-and-done proposition, nor does it by itself constitute an effective safety management system. If you are trying to build an employee-centric workplace, ensure positive employee experience and foster a culture of safety, then all your employees, including leaders and managers, need to be aligned and on the same page.
In addition to having a clear plan, using prevention through design techniques, and safety training sessions, organizations need to find ways to embed new employee safe work behaviors by delivering inspiring safety stories, communicating new safety programs, and sharing the company’s successes. Encourage engagement and participation from employees in the training methods.
Businesses will always experience safety challenges, but integrating these four best practices into your daily risk management regimen will ensure that your business has the tools to prevent a simple challenge from becoming a major disaster, already in its tool box.
THE RISK MATRIX Cutting-edge podcast on occupational safety and risk management. Hosted by industry titans: JAMES JUNKIN, MS, CSP, MSP,…
We’ll send you practical and insightful supply chain risk management info that can benefit your business. Plus, important company updates that keep you in the loop.