
An Integrated Approach to Worker Safety Helps Prevent Human Error
The oil and gas industry needs a new approach to safety that integrates preventative and corrective actions to keep workers safe on the job site.
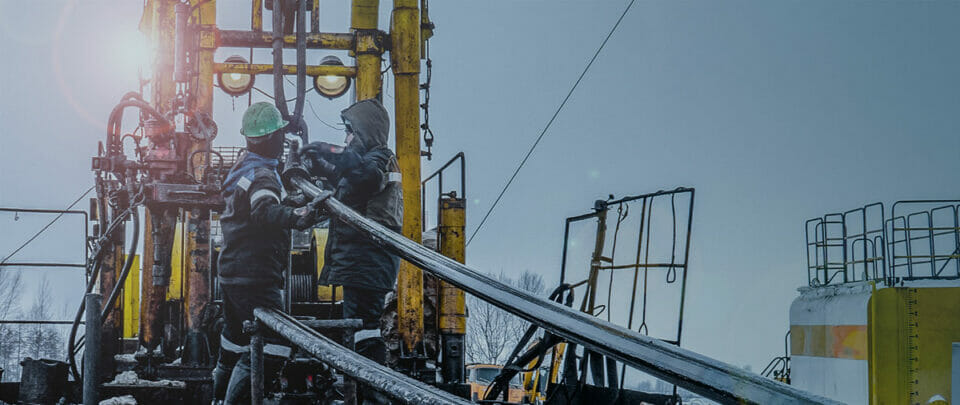
For many years the safety profession has taught that as many as 85% of workplace injuries and safety incidents can be attributed to human error. This has been largely discredited by current data and a better understanding of accident causation. However, the application of seeing the workforce as the cause of workplace injuries and illnesses, without ever considering other influencers such as error provoking tasks, poor design, faulty maintenance, fatigue, inadequate resources, and bad management decisions is alive and well. While the injury rate has trended down since 1993 according to the Bureau of Labor Statistics (BLS), the number of fatal and serious injuries (SIFs) has not. In order to reduce the number of SIFs in the oil and gas industry a change in the methods we are using must occur.
Over the years, a variety of safety approaches have been employed to combat injuries, including regulatory-based and behavior-based safety methods, as well as the implementation of safety management systems (SMS), and human performance assessment. However, a single approach to addressing these unsafe acts has not yet proven successful, particularly in addressing serious injuries and fatalities. That’s because human error does not occur in a vacuum. An array of external and organizational factors contribute to each situation.
The oil and gas industry must consider a new approach to safety and other causes of human error. Retraining and behavioral modification is often the default corrective action, but if error potential is designed into the work itself, it will prove ineffective. Hazards are best controlled in the planning and design of the work itself.
A new, integrated approach that focuses on bringing together human performance, safety management systems and behavioral approaches can build better and safer job sites supported by safe workers.
Benefits of an integrated approach to worker safety
Safety, especially in high-risk work environments, is complex. Unsafe acts in the workplace can be attributed to multiple causes. When an organization only uses one approach to analyze a failed safety system, related causes can be missed. You can also overlook a key component to future safety success: prevention. An integrated approach, with three steps, can help organizations look beyond corrective actions used only to address unsafe acts that have already taken place, and instead evaluate the systemic causes of these actions.
A true integrated approach to safety will master the trifecta of a human performance, safety management concepts and behavioral approaches.
Step 1
Human Performance Approach
To ensure the policies, processes, and procedures your organization puts in place to support workplace safety are effective, start with human performance. Here are the three primary steps to evaluating human performance when it comes to safety:
- Consider task demands, conditions, and timing that could explain unsafe acts. A multitude of conditions might cause workers to rush or get distracted while completing tasks. These include tasks occurring at the end of a shift or during a second shift when employees are more tired, high workloads, and monotonous duties. Changes in routine or unexpected equipment performance can cause confusion and quick decision making as well. Managing tasks for the first time or performing unfamiliar, infrequent or nonroutine tasks under pressure can also impact worker performance.
- Look for cognitive characteristics. This evaluation requires a deeper understanding of your workforce on the individual level. Not only should you consider the signs of tired, stressed, or sick employees, but also pre-existing characteristics such as overconfidence, biases, poor communication or problem-solving skills, and an understanding of risk.
- Address how these error precursors exist. Once you identify the precursors, you must pinpoint why they have, thus far, been allowed to exist within your organization. Ask yourself what structural deficiencies are at the root of these conditions? These could include unrealistic production schedules and poor task assignments from managers.
Step 2
Safety Management Systems (SMS) Concepts
A strategic SMS approach factors in process design and company procedure deficiencies, which play a key role in the occurrence of unsafe acts. By asking whether the process design prevented the worker from acting in a safe manner, the organization is looking for flaws within its own system to build more preventative methods in the future.
When process is identified as a factor in the occurrence of an unsafe act, a strong SMS approach triggers a risk assessment and a process change. It could also prompt a review of how an unsafe process was initially designed and how it passed any prior risk assessments.
Step 3
Behavioral Approaches
Behavioral approaches are the final building block to a successful integrated approach because they help you address long-term worker behaviors and mindsets as they relate to safety.
Many unsafe acts are not the result of negative perceptions or attitudes toward safety (remember error precursors). Identifying the triggers that may lead to unsafe acts can help shift the mindset around these triggers and ultimately lead to different outcomes. This approach could include establishing more positive consequences to safe practices and a more thorough understanding of risk throughout the organization. It has also been shown that a participatory approach to changing behavior can be successful by instituting feedback loops and reward systems to motivate individuals and build a team outlook on safety.