
Advanced Process Control: Optimizing Downstream Operations
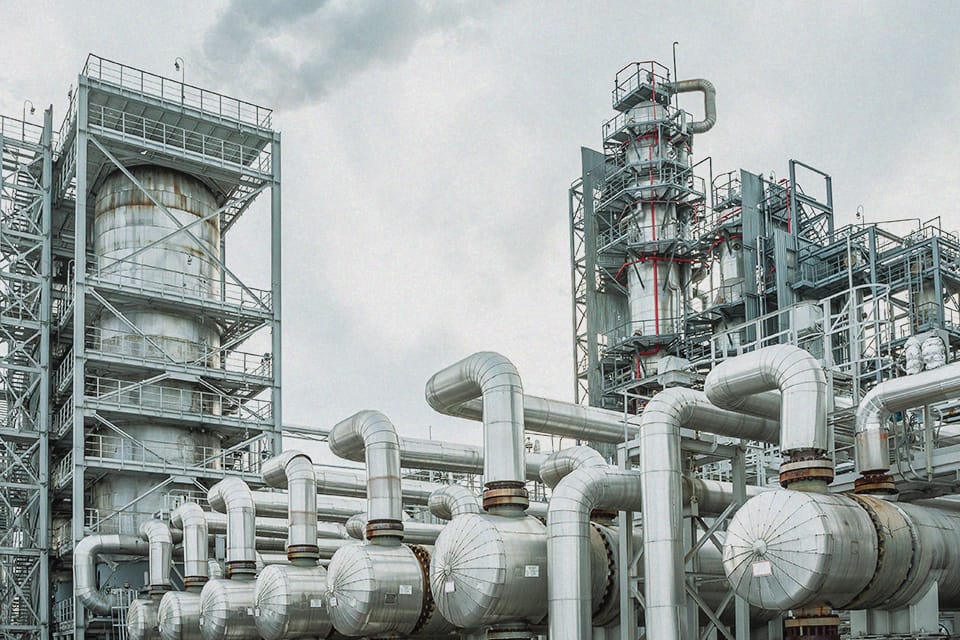
In today’s competitive downstream oil and gas industry, staying ahead of the curve requires constant innovation and optimization. Traditional process control systems can only take a company so far, and Advanced Process Control becomes vital to maximize performance and efficiency.
This article discusses the APC concept and its benefits, implementation strategies, and key components.
What Is Advanced Process Control?
At its core, Advanced Process Control (APC) involves optimizing control for the best performance possible. It drives better quality, less variability, higher throughput, and greater energy efficiency by utilizing specific automation tools, such as the following: tools like:
- Analytics
- Statistical modeling
- Model Predictive Control (MPC)
- Multiple loop control
Challenges of Implementing Advanced Process Control
However, implementing APC can be challenging and seem complex, especially for operations teams who are already stretched thin.
Understaffing and perceived complexity have convinced some that APC is beyond their means and capabilities, but that’s not necessarily the case. By asking the right questions about the process, management can understand APC and its importance in staying competitive in today’s environment.
How Advanced Process Control Optimizes Operating Conditions
Ways in which APC optimizing operation conditions in downstream oil and gas include the following:
Improving Process Efficiency
APC brings all regulatory control elements together to maximize automation and efficiency. However, it is not a one-size-fits-all solution and requires customization to each process, which is the key to maximizing efficiency.
Reducing Energy Consumption
APC minimizes wasted energy by keeping process variables as close to their optimal targets as possible. Improved efficiency and stability translate directly to energy savings, which is a necessity in today’s oil and gas environment.
Enhancing Product Quality
Consistency is critical for product quality, and that’s where APC shines. By reducing variability in the process, APC helps ensure that quality parameters remain on target. Those advanced algorithms and modeling capabilities keep the product within optimal specs more consistently than basic regulatory control ever could.
Increasing Production Throughput
APC can also help companies get the most out of their existing equipment by pushing the process to a manageable limit – without sacrificing quality or safety. APC’s dynamic optimization identifies opportunities to maximize production that would be missed by regulatory control alone.
The Role of Advanced Process Control in Digital Transformation
APC is integral to digital transportation – particularly in the downstream oil and gas sector. Its specific roles include the following:
Enabling Industry 4.0
Industry 4.0, the fourth industrial revolution, is all about decision-making and dynamic optimization. Sound familiar? That’s because it’s exactly what APC delivers. APC is a key enabling technology for Industry 4.0 initiatives in the process industries. It’s a core capability for any manufacturer serious about digital transformation.
Integrating with Existing Control Systems
A critical aspect of APC is that it can integrate with and leverage existing control systems and instrumentation, avoiding the need to rip out and replace anything. It can often be implemented using the control capabilities you already have in place, making it a cost-effective solution for optimization.
Leveraging Data Analytics
APC is also essential to turning data into actionable insights. It relies heavily on data analytics to build its process models and optimization algorithms and leverages that data to identify opportunities for improvement. And as Industry 4.0 drives even more digitalization and data collection, APC will become an even more powerful tool for oil and gas operations.
Enhancing Operational Agility
In today’s fast-paced market, agility is everything. Manufacturers must be able to pivot on a dime, and APC makes that possible. By enabling dynamic process optimization, APC allows companies to adjust operating targets and parameters as needed to maintain optimal performance, even in the face of change.
Key Components of Advanced Process Control Systems
The key components of an APC system are as follows:
Model Predictive Control
Model predictive control (MPC) is the proverbial brain of the operation. It uses dynamic models of the process to predict future behavior and proactively make control adjustments. This predictive approach is how APC can outperform traditional regulatory control and stays one step ahead, keeping the entire process on track.
Optimization Algorithms
At the center of APC are powerful optimization algorithms, continuously running analyses to maximize performance. They take into account several factors, including the following:
- The current state of the process
- The desired operating targets
- Any applicable constraints
Once these algorithms finish their analyses, they determine the optimal control actions to take.
Real-time Data Acquisition
However, none of this would be possible without real-time data. APC systems constantly collect data from the existing instrumentation and control systems. This real-time information flow keeps APC’s models and algorithms up to date and allows it to adjust to changing conditions on the fly dynamically.
User-friendly Interfaces
A good APC system needs to be user-friendly (despite its complexities), so the team responsible for running the process can interact with it effectively. APC software includes intuitive graphical displays, dashboards, and reports to promote a more seamless user experience.
These tools help users monitor performance and make informed decisions and allow engineers to maintain and update the APC application over time. These features allow the system to evolve as the process does.
Implementing Advanced Process Control at a Downstream Facility
Lastly, downstream companies need a roadmap for implementing an APC system. The steps to do so should include the following:
Assessing Process Control Needs
First, companies must assess their current process control situation and identify pain points and areas for improvement.
This is where an in-depth control study or audit might come into play: it can help management benchmark the current performance and pinpoint areas where APC could drive real results. For example, prime candidates for APC optimization might include any process units that are underperforming or highly variable.
Selecting the Right APC Solution
After identifying the need for APC, companies must select the right solution Key factors to consider when choosing an option include the following:
- Alignment with your existing control systems
- Scalability
- Ease of use
- Vendor support
Companies should choose a solution that can grow with them, meeting their current and future needs.
Integrating with Existing Systems
APC doesn’t exist in a vacuum and must integrate seamlessly with existing process control systems and IT infrastructure. Successful integration requires close collaboration among the APC vendor, automation engineers, and IT personnel.
Everyone needs to be on the same page to ensure a smooth integration. The goal is to realize the full benefits of APC without disrupting current operations.
Training Personnel
Implementing APC isn’t just about the technology—it’s also about the people who will be using it daily.
That’s why training is critical for optimal APC performance. The operators need to know how to interact with the APC interface, and the engineers need to know how to maintain and optimize the APC application over time.
The more comfortable and proficient the team is with the APC system, the more value a company can extract from it.
Combine Advanced Process Control with the Right Risk Management Solutions
Advanced process control is a powerful tool that can transform your downstream oil and gas operations. By optimizing control strategies, reducing variability, and improving efficiency, you can achieve significant benefits for your bottom line. Also, always remember that implementing advanced process control isn’t a one-and-done deal. It’s a continuous journey of improvement, adaptation, and growth. As your processes evolve, so should your control strategies.
However, and while understanding APC is a critical first step, it is just one piece of the puzzle. For true operational excellence, you also need robust supply chain risk management and process safety management solutions that meet the specific needs of your worksite.
Consider working with us to configure a solution that enhances operational efficiency and improves safety performance.
Contact us today to learn more.