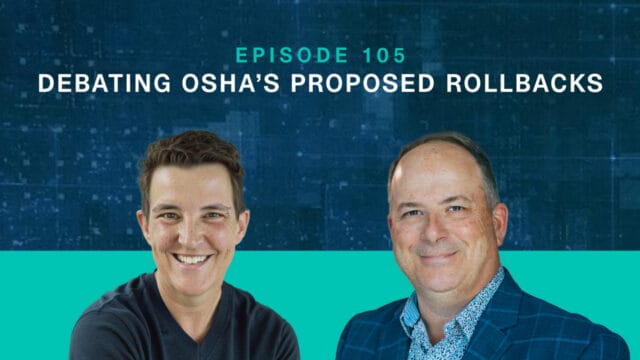
Season 2 Kickoff: Debating OSHA’s Proposed Rollbacks | The Risk Matrix Episode 105
THE RISK MATRIX Cutting-edge podcast on occupational safety and risk management. Hosted by industry titans: JAMES JUNKIN, MS, CSP, MSP,…
Companies should design a plan to meet and maintain OSHA compliance to safeguard workers from harm and avoid unnecessary liabilities.
The United States Congress passed the Occupational Safety and Health Act (OSHA) in 1970, establishing and enforcing standards that guarantee a safer and healthier job site for all workers. And for companies employing contractors and subcontractors on the work site, OSHA compliance is critical, and following all applicable standards helps ensure those sites are free from significant risks that could endanger personnel.
This article discusses seven steps all companies should take to preserve OSHA compliance.
Routine inspections are essential for companies to support OSHA compliance and safe workplace environments. These inspections ensure continuing compliance by:
Also, by actively monitoring, businesses show their commitment to worker welfare and legal compliance, fostering a culture of safety that boosts morale and productivity.
A successful health and safety program relies on well-written policies that specify the duties of both contractors and subcontractors. And all workers new to the job site should receive these documents at orientation to ensure they understand their responsibilities.
However, developing the best policies is a two-way street. The employer is ultimately responsible for the program’s terms and conditions, but workers on the ground are often better positioned to supply actionable insights that optimize safety procedures.
Therefore, companies might ask workers for their opinions on processes and procedures before finalizing documentation. Businesses must tailor policies specific to their work sites, and they will receive no better insight than that from workers with on-site experience.
Many companies store hazardous chemicals on their worksites. And OSHA requires they develop a hazard communication program to ensure everyone in contact with these chemicals understands the risks.
The critical components of this program include but are not limited to the following:
By implementing these components effectively, employers can ensure that their hazard communication program follows OSHA’s standards.
OSHA training helps workers become more aware of job site hazards and the safeguards to maintain safety. It also allows them to run more productively and efficiently with less chance of injury or accident.
More specifically, contractors and subcontractors on the ground will gain the following through OSHA training:
The first step of workplace safety and hazard prevention is protection, and an effective way to safeguard workers is by providing sufficient safety supplies.
These items might include personal protective equipment (PPE), including the following:
However, companies should conduct a thorough workplace hazard assessment before supplying PPE to determine the specific types needed. This assessment should identify potential hazards, assess the severity of risks, and guide the choice of the proper PPE for each situation.
Additionally, ensure that PPE is properly fitted, maintained, and worn according to manufacturer guidelines and OSHA regulations.
Appointing a responsible party to oversee compliance with OSHA regulations is essential as it provides focused leadership and accountability in supporting a safe and healthy work environment. This designated individual or team has the expertise to:
Ultimately, their role cultivates a safety culture, showing the company’s commitment to worker well-being while enhancing regulatory compliance and inspection readiness.
Maintaining detailed records is also critical, as it helps companies prove their commitment to safety, track safety efforts, and supply a clear history of compliance initiatives.
Key records essential for compliance include but are not limited to the following:
To maintain OSHA compliance, companies must empower on-site teams to report potential problems, carry out everyday tasks, and keep management informed of crucial developments. And to do this effectively, they must implement the industry’s premier risk management tools that help workers understand OSHA requirements, why they are necessary, and what it takes to comply.
Work with us to configure a solution that addresses site-specific needs and promotes a working environment that fosters consistent compliance with OSHA regulations.
Contact us today to learn more.
THE RISK MATRIX Cutting-edge podcast on occupational safety and risk management. Hosted by industry titans: JAMES JUNKIN, MS, CSP, MSP,…
We’ll send you practical and insightful supply chain risk management info that can benefit your business. Plus, important company updates that keep you in the loop.