
6 Steps to OSHA Pipeline Compliance
Whether it’s a leak detected on a pipeline that led to a significant diesel spill, or an explosion that resulted in multiple employee injuries or even deaths, pipeline accidents wreak havoc on your business, your workers and the local community.
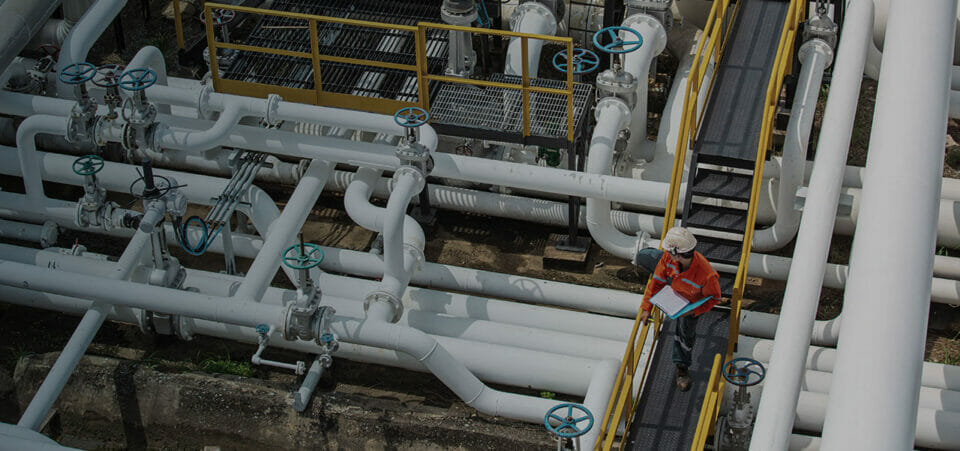
Whether it’s a leak detected on a pipeline that led to a significant diesel spill, or an explosion that resulted in multiple employee injuries or even deaths, pipeline accidents wreak havoc on your business, your workers and the local community.
Since 1987, the U.S. Department of Transportation’s Pipeline and Hazardous Materials Safety Administration (PHMSA)[1] has documented more than 3,200 serious and significant incidents where a gas pipeline damaged or ruptured, leaking hazardous gas into the environment and in some cases, causing explosions, fires, injury, and death.
To best protect against these highly costly and dangerous events, here is a six-step guide to achieving Occupational Safety and Health Administration (OSHA) pipeline compliance.
1. Identify the hazards associated with job tasks and scope of work and implement controls.
This will include locations for excavation and trenching; hot work; rigging and crane operations; lock out, tag out (LOTO); hot tapping, and the like.
Employees’ potential for exposure to those hazards must be determined and operators and contractors need to establish how to optimally protect and shield workers from exposure. To do this, a hierarchy of controls[2] should be implemented, which includes using interim controls or a combination of controls to ensure safety.
2. Develop executable company-specific policies and procedures.
While anyone can Google “confined space policy and procedure” and download a list of boxes to check, businesses looking to optimize worker safety and protection will customize their safety rules to reflect the needs of both their business and then, more specifically, the jobsite.
Occupational safety and health policies and procedures represent the foundation of a functioning and executable safety management system. Work with your team to develop customized policies and procedures that meet regulatory standards, third-party verification requirements, and industry best practices.
Custom-written safety programs ensure top management involvement, employee participation, and continuous feedback loops for improvement, such as the Plan-Do-Check-Act (PDCA), and fit well with established safety management systems such as ANSI/ASSP Z-10-2012 (R2017) and ISO 45001.
3. Develop a matrix that includes orientation, awareness, and end-user training.
A basic course offers orientation and awareness training. While important in establishing a foundation for safe work and future training, this is not enough to be compliant with regulations and to ensure safety in the process. For example, employees using LOTO, confined space operations, fall protection, and wearing respiratory protection must be trained beyond the awareness level according to OSHA [3].
4. Document your operator qualifications (OQ) program.
It’s important to distinguish between competent and qualified. It’s one thing for an operator to be trained and considered competent to read a gauge, for example. But per the PHMSA[4], pipeline operators must have a certain number of employees on staff who have been “adequately trained to recognize and react to abnormal operating conditions that may occur while performing specific tasks.” This includes an OQ program with a written plan, an applicable task list, training, and qualification requirements, and ensuring that contractors and vendors comply with these program requirements.
5. Conduct incident and accident investigations, with appropriate root cause analysis.
To ensure that incidents and accidents don’t happen again, companies must determine what happened, why it happened, and put corrective actions in place. Even if there was no negative outcome, incidents still need to be documented. For example, one operator accidentally passed a suspended load with a crane over employees. Fortunately, nothing fell and no one got hurt, but it could have. In another example, workers failed to wear their personal protective equipment. While not wearing eye gear doesn’t mean an eye will get poked out, it could happen.
What separates a near miss from an actual incident from occurring? Luck, most of the time. When you vigorously investigate near misses to determine what happened, why it happened, and put corrective actions in place so it doesn’t happen again, you’re more likely to succeed.
6. Institute a Plan, Do, Check, Act (PDCA) approach.
The Plan, Do, Check, Act approach achieves a balance between the systems and behavioral aspects of management. It also treats health and safety management as an integral part of good management generally, rather than as a stand-alone system.
PDCA is a continuous improvement approach found in most safety management systems that directs management to plan the work, do the work, check to make sure the work is being done safely and make changes if required [5].
[1] U.S. Department of Transportation Pipeline and Hazardous Materials Safety Administration “Pipeline Incident 20 Year Trends,” February 2021.
[2] Occupational Safety and Health Administration “Recommended Practices for Safety and Health Programs”
[3] OSHA “Training Requirements in OSHA Standards.”
[4] U.S. Department of Transportation Pipeline and Hazardous Materials Safety Administration “About Operator Qualification.” [5] Health and Safety Executive “A Brief Summary of Plan, Do, Check, Act.”