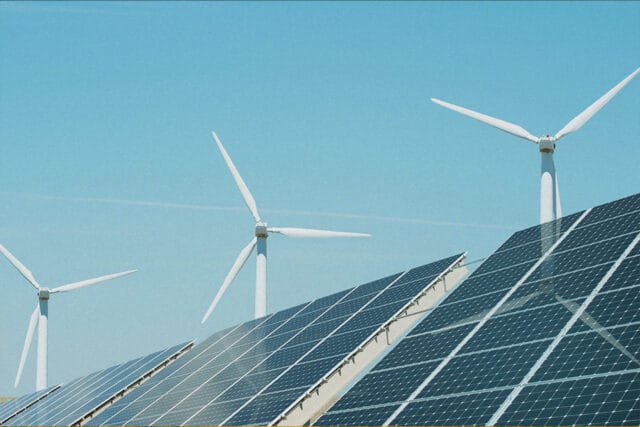
7 Tips for Maintaining OSHA Compliance
Companies should design a plan to meet and maintain OSHA compliance to safeguard workers from harm and avoid unnecessary liabilities.
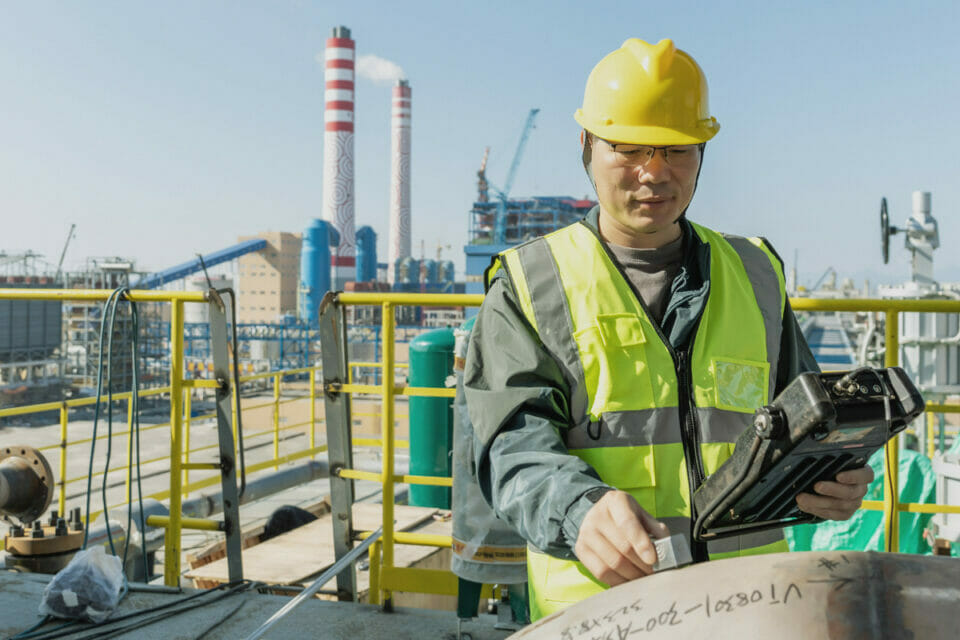
The United States Congress passed the Occupational Safety and Health Act (OSHA) in 1970, establishing and enforcing standards that guarantee a safer and healthier job site for all workers. And for companies employing contractors and subcontractors on the work site, OSHA compliance is critical, and following all applicable standards helps ensure those sites are free from significant risks that could endanger personnel.
This article discusses seven steps all companies should take to preserve OSHA compliance.
OSHA Compliance: 7 Steps to Consider
1. Conduct Regular Inspections
Routine inspections are essential for companies to support OSHA compliance and safe workplace environments. These inspections ensure continuing compliance by:
- Systematically finding potential risks
- Evaluating the efficacy of safety procedures
- Ensuring ongoing OSHA compliance in the face of change legislation and working conditions
- Improving safety precautions for new equipment
Also, by actively monitoring, businesses show their commitment to worker welfare and legal compliance, fostering a culture of safety that boosts morale and productivity.
2. Collaborate with Works to Develop Safety Policies
A successful health and safety program relies on well-written policies that specify the duties of both contractors and subcontractors. And all workers new to the job site should receive these documents at orientation to ensure they understand their responsibilities.
However, developing the best policies is a two-way street. The employer is ultimately responsible for the program’s terms and conditions, but workers on the ground are often better positioned to supply actionable insights that optimize safety procedures.
Therefore, companies might ask workers for their opinions on processes and procedures before finalizing documentation. Businesses must tailor policies specific to their work sites, and they will receive no better insight than that from workers with on-site experience.
3. Build a Hazard Communication Plan
Many companies store hazardous chemicals on their worksites. And OSHA requires they develop a hazard communication program to ensure everyone in contact with these chemicals understands the risks.
The critical components of this program include but are not limited to the following:
- A written statement outlining how the company will follow the standard’s requirements
- An inventory listing hazardous chemicals present in the workplace
- Product labels specifying the product’s identity, hazard statements, and the supplier’s identity
- An ongoing review of the program supplying updates to chemicals, processes, or regulations that could affect hazard communication
By implementing these components effectively, employers can ensure that their hazard communication program follows OSHA’s standards.
4. Provide Ongoing OSHA Compliance Training
OSHA training helps workers become more aware of job site hazards and the safeguards to maintain safety. It also allows them to run more productively and efficiently with less chance of injury or accident.
More specifically, contractors and subcontractors on the ground will gain the following through OSHA training:
- The required specialized training to perform tasks with particular risks
- The necessary expertise to carry out their duties without risk to themselves or their team members
- The ability to recognize and report workplace dangers and learn to control them better in the future
5. Ensure there are enough safety supplies
The first step of workplace safety and hazard prevention is protection, and an effective way to safeguard workers is by providing sufficient safety supplies.
These items might include personal protective equipment (PPE), including the following:
- Safety glasses and goggles
- Face shields
- Hard hats
- Earplugs and earmuffs
- Respirators
- Gloves
- Safety shoes
- Chemical and electrical protective clothing
However, companies should conduct a thorough workplace hazard assessment before supplying PPE to determine the specific types needed. This assessment should identify potential hazards, assess the severity of risks, and guide the choice of the proper PPE for each situation.
Additionally, ensure that PPE is properly fitted, maintained, and worn according to manufacturer guidelines and OSHA regulations.
6. Appoint a Responsible Party
Appointing a responsible party to oversee compliance with OSHA regulations is essential as it provides focused leadership and accountability in supporting a safe and healthy work environment. This designated individual or team has the expertise to:
- Navigate complex OSHA regulations to proper interpretation and implementation of safety measures.
- Coordinate efforts across departments to foster consistency in safety protocols and efficient communication.
- Drive continuous improvement
- Prepare the company for potential emergencies by watching trends and addressing risks promptly
Ultimately, their role cultivates a safety culture, showing the company’s commitment to worker well-being while enhancing regulatory compliance and inspection readiness.
7. Keep Detailed Records
Maintaining detailed records is also critical, as it helps companies prove their commitment to safety, track safety efforts, and supply a clear history of compliance initiatives.
Key records essential for compliance include but are not limited to the following:
- Injury and Illness records (OSHA Form 300 Series) that help companies track the frequency and nature of workplace injuries and illnesses, identifying trends and areas for improvement
- Training records that employees have received the necessary training to perform their jobs safely
- Inspection Reports that show companies are actively identifying and addressing potential safety risks
- PPE documentation that records the issuance and maintenance of personal protective equipment
- Emergency Response Plans that demonstrate the company’s preparedness for various emergency scenarios
Leveraging the Right Tools is Critical to Maintaining OSHA Compliance
To maintain OSHA compliance, companies must empower on-site teams to report potential problems, carry out everyday tasks, and keep management informed of crucial developments. And to do this effectively, they must implement the industry’s premier risk management tools that help workers understand OSHA requirements, why they are necessary, and what it takes to comply.
Work with us to configure a solution that addresses site-specific needs and promotes a working environment that fosters consistent compliance with OSHA regulations.
Contact us today to learn more.