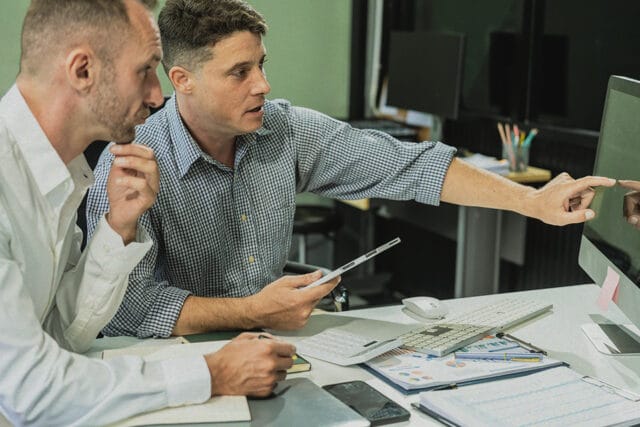
4 Fundamentals to an Effective PSM Program
Creating a culture of safety around PSM is critical to OSHA compliance. Doing it right keeps your entire workforce safe, from employees to contract workers — and from the top all the way down.
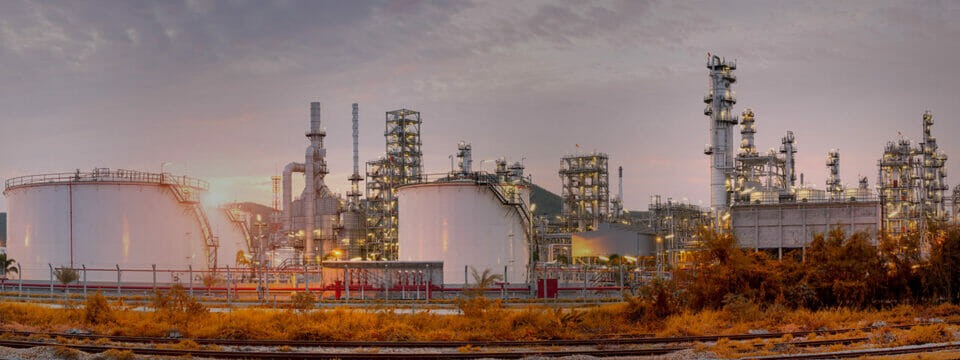
In safety-related accidents, human error is almost always to blame. And the consequences are grave. It gets increasingly more complicated when contractors are the ones doing your work.
A recent contractor management study conducted by Veriforce found that as many as 91% of businesses employing skilled workers use contractors or temporary help to meet daily project demands. It’s not surprising, as worker shortages permeate skilled industries today.
Take chemical plants, for example. Across the globe, they make headlines too often after an explosion, an unplanned release of gas or an oil leak. According to the Houston Chronicle1, chemical explosions in the Houston area occur on average once every six weeks. While that number may be high due to the city’s concentration of oil and gas operations, when the result is almost certainly fatalities, trapped workers, miles of shelter in place orders and reputational risk, that number is far too high.
Enter: PSM, or Process Safety Management, OSHA’s 14 preventative elements that seek to rid hazardous chemical operations of disaster through regulatory compliance.
While PSM’s 14 elements are important and known safety principles, most businesses aren’t solving for them the way they need to be. That’s because it’s hard enough for employers to implement best practices in risk management safety across an internal worker base when employees feel close to a business’ mission. How can a chemical plant implement the same safety message across hundreds of contract workers from dozens of small contract firms?
It’s nearly impossible.
What does it take to do PSM right — across your entire workforce?
The answer is four-fold: Formal policies and procedures, comprehensive internal and contractor worker training, and PSM audits — with all contractor-specific aspects managed and documented in a digital supply chain management solution.
1. PSM policies and procedures.
Creating standard operating procedures (SOPs) around your PSM compliance helps workers in the field carry out your PSM policies and procedures.
2. Comprehensive training.
PSM training is critical to compliance — and ensuring your work gets done safely. Take a new contractor who enters your chemical plant to do some electrical work. Since evacuation routes and procedures are unique to each facility, new contractors should be trained on evacuation day one, per PSM Element #4, or Operating Procedures. Sounds obvious, right? The question is: Does the contractor actually get trained? And if he/she does, how is that training documented?
3. The PSM audit.
Completed by a qualified third-party auditor every three years, the PSM audit should include an evaluation of how your facility carries out all 14 principles. Audit documentation should be in a form that is easily accessible.
4. Digital documentation.
No employer or contractor firm is willfully neglecting their responsibilities, whether it be PSM or something tangentially related, and yet 91% of employers are still documenting contract workers and their credentials, including PSM training, on spreadsheets or simple pen and paper subject to human error and nearly impossible to maintain with a staff of hundreds of workers.
PSM is a never-ending job. To maintain optimal performance of your PSM program across your internal and external workforce, it must be top of mind constantly. Executive leadership has to support it; your workforce needs to remain engaged, informed and trained on it; and you must ensure that workers feel fulfilled, protected and motivated to uphold it.
This means there’s a huge cultural and leadership component to PSM. How do you apply 14 PSM safety elements to a workforce that doesn’t report to you and doesn’t hear your leaders talking about it in all-company meetings? When 50% or more of your workforce is contractor contingent, you must be incredibly intentional in building in PSM touchpoints.
Put simply, PSM requires a top-down approach. Like many other corporate health, safety and environment (HSE) initiatives, PSM is a box that can’t just be “checked,” but must be continually attained, and anchored in the quest to send every worker home at the end of each night to do it all over again the next day.
When leaders see PSM as a key directive under the corporate HSE umbrella and prioritize it as such, compliance can be achieved. Those who hire and partner with your business will want to know that PSM is something you and your entire company have rallied around. When you champion these four aspects of PSM compliance, they’ll want to rally around you too.
1 Houston Chronicle. “Chemical Breakdown”
How effective is your PSM program?
For 30 years, Veriforce has helped hiring clients and contractors understand regulatory requirements and compliance; reducing worksite risks.