
2025 Outlook for OQ and Tools to Manage the Skills Gap and Compliance in the Midstream Industry
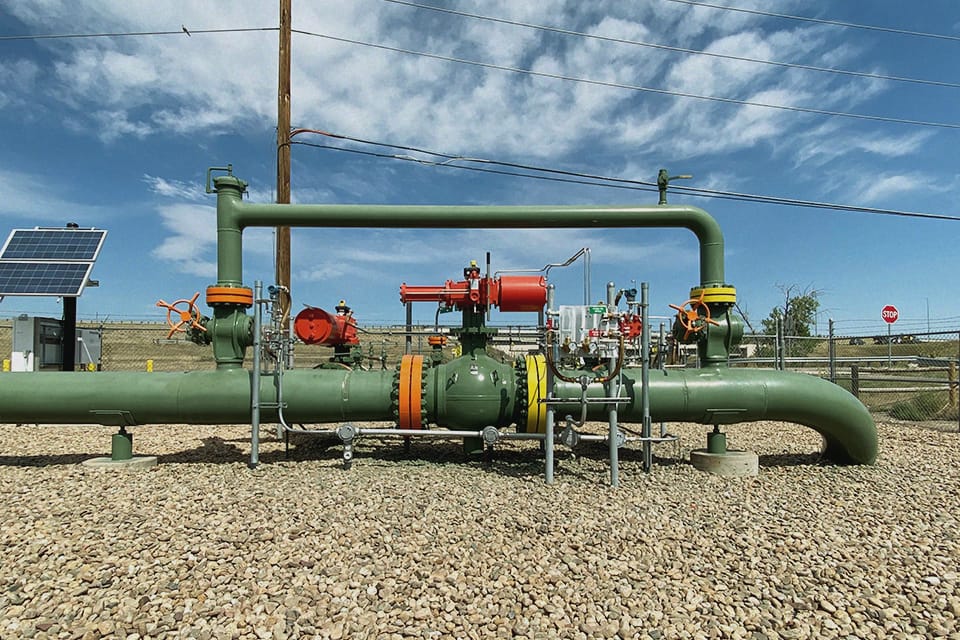
As we step into 2025, the midstream industry faces a pivotal moment in its journey toward operational excellence and regulatory compliance. Operator Qualification (OQ) programs, which are critical to ensuring the safety and reliability of pipeline operations, are at the forefront of this transformation. With a growing skills gap due to an aging workforce, evolving regulatory requirements, and increasing operational complexities, midstream companies must take proactive steps to understand, own, and optimize their OQ programs.
This article explores the 2025 outlook for OQ, the challenges posed by a workforce shortage, and the importance of companies taking ownership of their OQ programs to ensure safety and compliance.
Adapting to Change: Why a Solid OQ Program is Essential
It doesn’t seem that long ago since PHMSA released the new OQ FAQs in 2022. While FAQs don’t carry the weight of the existing regulations, they still help provide guidance around complying with the legacy rule. FAQs 7 and 8 were revised with new training guidelines that provide more clarity around training frequency, depth, and delivery.
States are required to follow federal regulations but are also authorized to go above and beyond. New York’s new OQ rule, announced in 2022, is a great example of this. There are several elements to this state-level rule including implementing a 48-hour delay between training and qualification – no longer just testing a worker’s short-term memory.
Changes to regulations are done for a reason but keeping up with them can be a challenge, which is why a third-party software solution is the key to compliance. Furthermore, it’s not just the hiring company that needs to ensure they have a defensible OQ program, but their contractors as well.
Ensuring OQ program alignment between employees and contractors is a significant challenge for pipeline companies, as inconsistencies in training, evaluation, and compliance standards can lead to safety risks and regulatory gaps. As stated in PHMSA’s OQ FAQ 2, contractors are not required to have a written OQ program. The onus is on the operator to ensure that “any individuals who perform covered tasks on the operator’s pipeline system, whether contractors or operator personnel, meet the requirements of the operator’s OQ program. If contractors have their own written OQ program, operators must verify that it meets the requirements of the operator’s OQ program”.
A third-party OQ software solution helps solve this challenge by:
- Simplifying OQ project management by easily setting up projects, OQ tasks, storing and accessing all documents, and overseeing contractor assignments.
- Eliminating paper training forms with a digital ‘record of training’ document.
- Offering a Field Verification Report to provide operating clients and contractors with the extra layer of verification information necessary to ensure workers have the qualifications, training, and certifications to be ready to work on the job site.
The Growing Skills Gap: A Looming Challenge for the Midstream Industry
One of the most pressing issues facing the midstream industry in 2025 is the retirement of a significant portion of its skilled workforce. This wave of retirements is creating a skills gap that threatens to disrupt operations and compromise safety if not addressed effectively. The loss of experienced operators means more than just a reduction in headcount; it represents the departure of decades of institutional knowledge, hands-on expertise, and problem-solving skills.
These seasoned professionals have been the backbone of pipeline operations, ensuring that critical tasks are performed safely and efficiently. As they exit the workforce, companies are left with the challenge of training and qualifying new operators to fill these roles. The skills gap is further exacerbated by the increasing complexity of pipeline operations.
Advances in technology, such as the integration of automation, data analytics, and remote monitoring, require operators to possess a broader skill set than ever before. New hires must not only understand the fundamentals of pipeline operations but also be adept at using advanced tools and systems to maintain safety and efficiency.
To bridge this gap, midstream companies must invest in comprehensive training and qualification programs that equip new operators with the skills and knowledge they need to succeed.
The Importance of Understanding and Owning Your OQ Program
In the face of these challenges, it is more important than ever for midstream companies to take ownership of their Operator Qualification programs, while working in partnership with a third-party solution provider. OQ programs are not just a regulatory requirement; they are a cornerstone of pipeline safety and operational integrity. Companies that view OQ as a mere compliance checkbox are missing the opportunity to leverage these programs as a strategic asset.
Key Elements of Owning Your OQ Program
- Develop qualification standards tailored to your pipeline system and operational risks.
- Take responsibility for training and evaluation processes, whether conducted in-house or through third-party providers.
- Align OQ programs with your company’s safety culture and operational goals.
- Have a team of experts in your corner.
A well-designed OQ program should be tailored to the specific needs of your organization, taking into account the unique characteristics of your pipeline system, the tasks performed by your operators, and the risks associated with those tasks. This requires a deep understanding of regulatory requirements, industry best practices, and the latest advancements in training and qualification methodologies.
That’s when you need the BEST team of experts on your side. With Veriforce’s team of OQ experts, you’ll never miss a new regulation, and you can feel confident you have the most defensible OQ program possible. Plus, Veriforce’s Common Covered Task List Steering Committee works in collaboration with industry leaders to create a common covered task list and associated criteria. This “dream team” of experts, who consistently collaborate with the industry, pulls all the potential fragments of your OQ program together.
By taking ownership of your OQ program, while leveraging technology and teaming up with experts, you can ensure that it aligns with your company’s safety culture and operational goals. This proactive approach not only enhances compliance but also fosters a culture of continuous improvement, where operators are empowered to perform their duties safely and effectively.
The Role of Technology in Modernizing OQ Programs
As we look ahead to 2025, technology will play an increasingly important role in modernizing OQ programs and addressing the skills gap. Digital tools and platforms are transforming the way companies train, evaluate, and qualify their operators, making it easier to deliver consistent, high-quality training across geographically dispersed teams.
E-Learning Platforms: Allows operators to complete training modules at their own pace and on their own schedule. These platforms can be customized to include interactive elements, such as simulations and quizzes, to enhance engagement and retention. Additionally, they provide companies with valuable data on operator performance, enabling them to identify areas for improvement and tailor training programs accordingly.
Virtual Reality and Augmented Reality: These technologies have evolved quickly and allow operators to practice complex tasks in a safe, controlled environment, reducing the risk of accidents and improving confidence. For example, an operator could use VR to simulate the process of inspecting a pipeline or responding to an emergency, gaining valuable experience without the need for physical equipment. But it’s important to point out that while VR has its place in a training program, nothing beats hands-on learning in the field on an actual pipeline. It is crucial to have both technological and experiential learning methods.
Data Analytics: By analyzing data from training sessions, evaluations, and real-world operations, companies can gain insights into operator performance and identify trends that may indicate a need for additional training or support. This approach enables companies to make informed decisions about their OQ programs and continuously improve their effectiveness.
Ensuring Safety Through a Culture of Accountability
At its core, an effective OQ program is about more than just compliance; it’s about fostering a culture of accountability and safety. Every operator, from entry-level technicians to seasoned supervisors, must understand the importance of their role in maintaining the integrity of the pipeline system. This requires clear communication, ongoing training, and a commitment to continuous improvement.
Midstream companies must also recognize that safety is a shared responsibility. While operators are responsible for performing their tasks safely and under established procedures, management must provide the tools, resources, and support needed to ensure success. This includes investing in training and qualification programs, as well as creating an environment where operators feel comfortable reporting safety concerns and suggesting improvements.
By taking ownership of their OQ programs and prioritizing safety, midstream companies can not only meet regulatory requirements but also build a reputation as industry leaders. In an era of increasing scrutiny and public awareness, this commitment to safety and accountability is more important than ever.
A Defensible OQ Program Requires the Right Partner
As we look ahead to 2025, the midstream industry must confront the challenges posed by workforce retirements, technological advancements, and evolving regulatory requirements.
Operator Qualification programs will play a critical role in addressing these challenges, ensuring that operators are equipped with the skills and knowledge they need to perform their duties safely and effectively. As such, midstream companies must take ownership of their OQ programs, leveraging technology and data to modernize training and evaluation processes. By doing so, they can bridge the skills gap, enhance compliance, and foster a culture of safety and accountability.
The future of Operator Qualification is not just about meeting regulatory requirements; it’s about building a safer, more resilient midstream industry. By investing in their OQ programs today, companies can ensure that they are prepared for the challenges and opportunities of tomorrow.
At Veriforce, we are committed to helping midstream companies navigate the complexities of Operator Qualification and achieve their safety and compliance goals. But don’t just take our word for it. Read this case study about how Kings Mountain Natural Gas experienced huge improvements to its OQ program after switching to Veriforce.
Contact us today for a free consultation to assess your OQ needs and explore how Veriforce can help you streamline your qualification process and close the skills gap in your workforce.